K-Rock +
Automotive
The automotive industry has experienced tremendous growth in recent decades. It is also distinguished by high competitiveness and the ongoing need to contain production costs.
The industry has long been at the forefront of the development of personal protective equipment, particularly items designed for the upper limbs, since hands and arms are essential in vehicle manufacturing and assembly lines.
This led Juba to analyse sector-specific occupational risks and develop gloves to preserve the health and safety of automotive industry workers.
Here is our wide range of models designed for the industry, organised by purpose and the protection needs of the person using them.
Receiving and parts classification
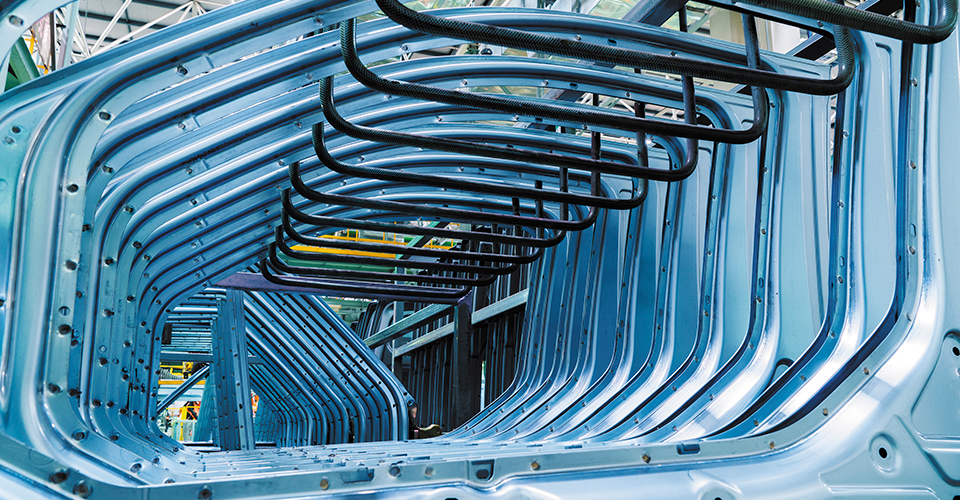
The vehicle parts in today's automotive production processes are manufactured in different specialised plants. Logistics and inspection tasks are performed there and the most common processes are loading and unloading received parts, handling packaging and strapping, and driving vehicles. These tasks are sometimes performed using touch devices and at times outdoors. This involves protecting operators in these departments from micro-cuts, abrasion and cold environments in winter and places with more extreme weather.
Juba has designed 20 different references in line with the protection needs of each worker and product handled
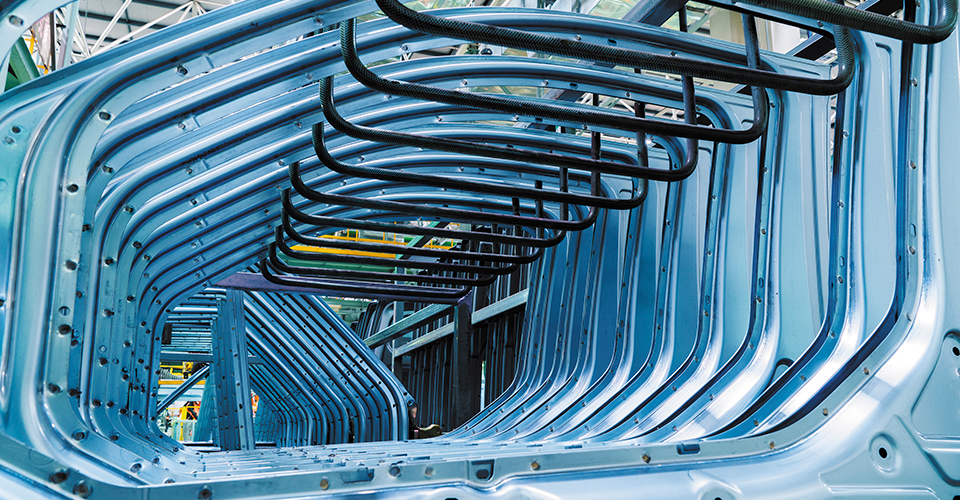
Gloves by phases
Logistics
General handling and the use of touch devices in cold environments
Inspection
Receiving and checking materials in clean areas with touch and no footprint
Quality review of materials received with a high level of touch
Quality review of materials received
Inspection of materials with a risk of cutting
Inspection of materials with no footprint
Metal part cutting and stamping
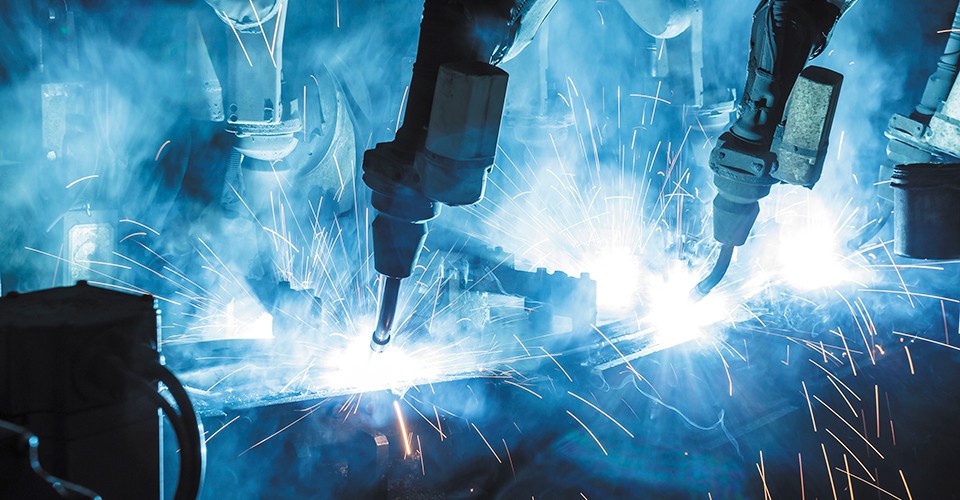
Cutting and stamping work involves heavy-duty handling tasks through to final part preparation. There is also a risk of cutting from the sharp edges of a part and pricking from possible burrs. Operators sometimes work in a dry environment but in many cases the parts are oiled, which entails a risk of them slipping when handled.
At Juba we have selected a dozen gloves for this section of the assembly line that care for workers by providing high levels of protection against cutting and abrasion and good grip in dry and oiled environments.
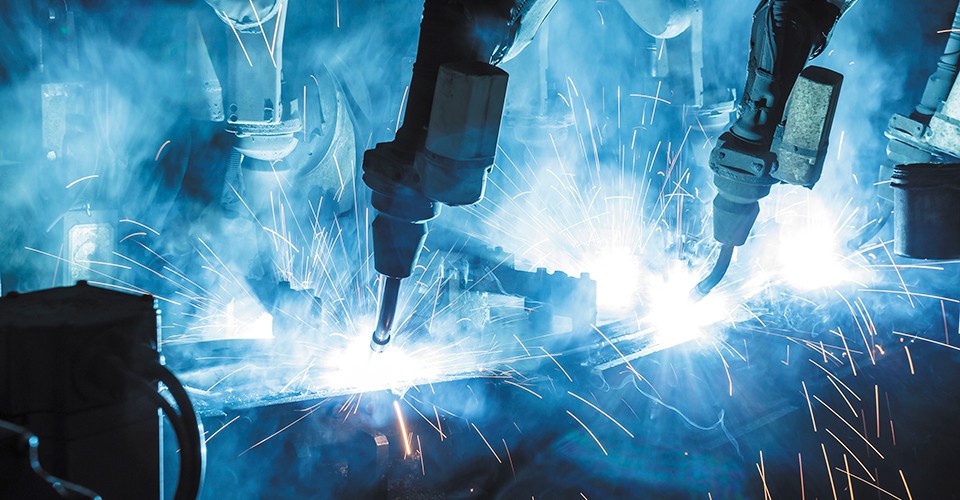
Gloves by phases
Risk of cutting
Stamping process with oiled parts
Maximum protection against abrasion, cutting and piercing
Chassis and body assembly
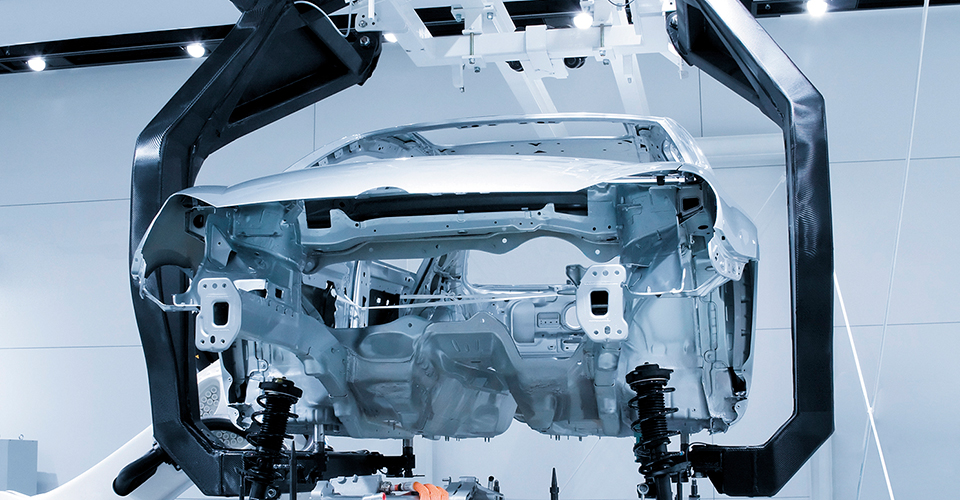
The preparation of vehicle structure assemblies and subassemblies involves manual fitting, the handling of large parts and welding and riveting operations. Workers are therefore exposed to mechanical risks such as cuts, impacts, thermal risks due to contact heat and hot sparks or damage from power or pneumatic tool vibrations.
At Juba we recommend up to 23 models depending on the risk (cutting, heat, vibration) and needs (touch, handling of oiled parts…).
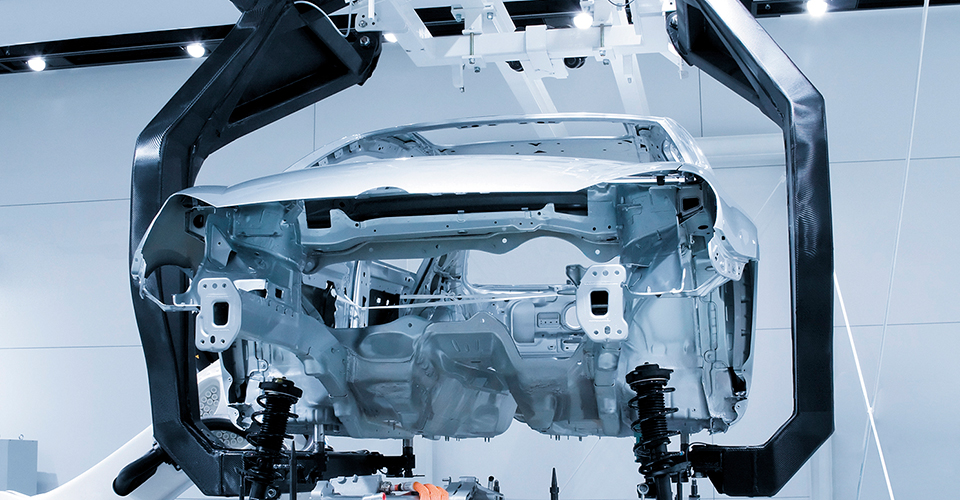
Gloves by phases
Handling with a risk of cutting
Vibration
Handling of electric/pneumatic vibrating tools
Handling with a risk of cutting and/or contact heat risk
Handling of parts with a medium risk of cutting and contact heat risk and/or lightly oiled parts
Handling of heavy parts with a high risk of cutting
Paint
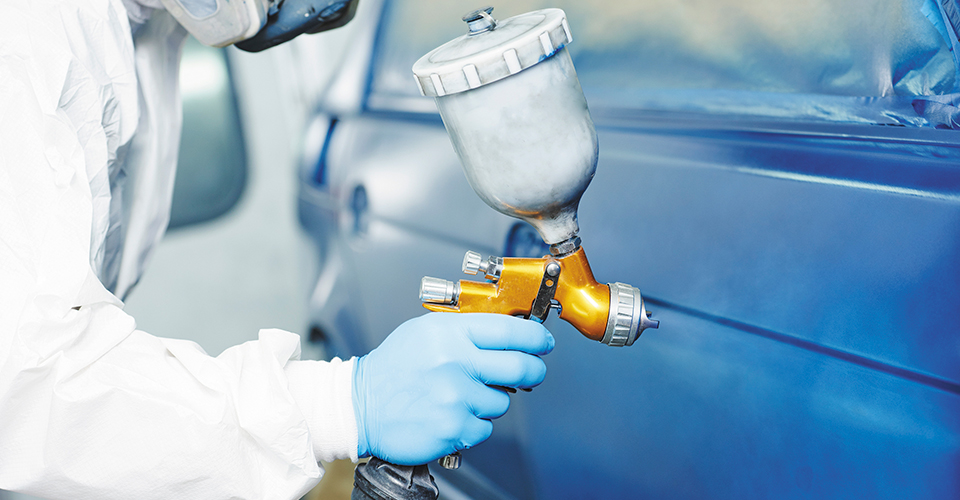
The final finish of the part involves fundamental subprocesses to prolong its life: chemical immersion anti-corrosion treatments, primer, sealing and finally painting. The painting section is highly automated in today’s manufacturing processes. Manual operations are usually limited to machine and room supervision, servicing, maintenance and cleaning, and these produce risks from exposure to chemicals.
At Juba we suggest you consult the chemical resistance chart or preferably our technical staff. We will help you choose the glove/s you need based on the chemicals used. Here is a selection of 11 gloves resistant to acids, inorganic bases, mineral oils, cutting fluids, solvents and paints.
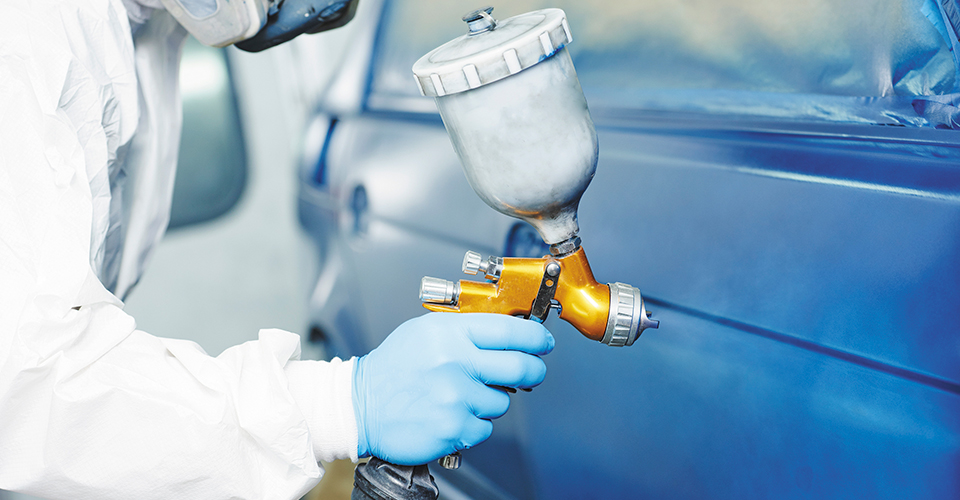
Gloves by phases
Chemical risk
Mechanical equipment assembly
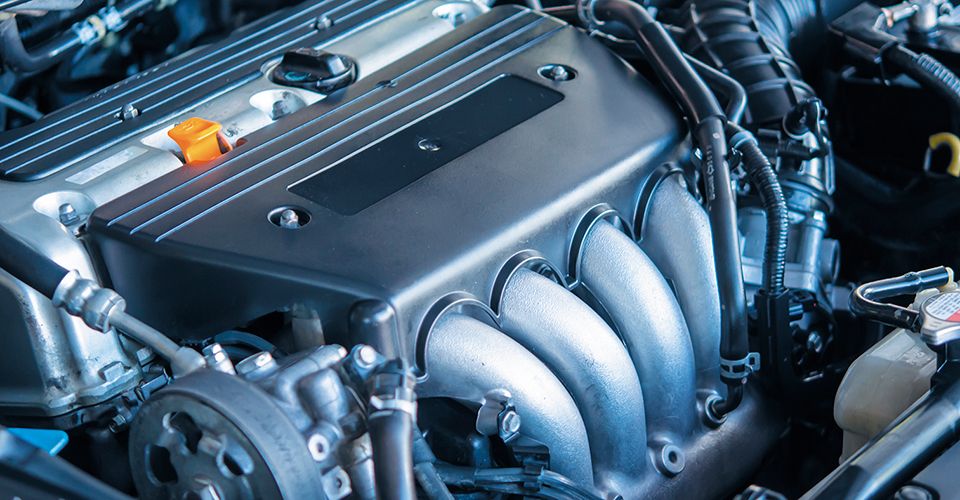
Most operations in the assembly section take place in a clean, dry environment. This section requires direct worker action. The highest level of touch is required, combined with medium and high levels of abrasion and cutting protection due to the sharp edges of some body components. Sometimes work is done with hot, oiled parts. Furthermore, circuit fluid-filling operations require protection against chemicals.
At Juba we have selected 23 models for the assembly section both for handling with a risk of cutting or impact and for people working with vibrating tools or in contact with chemicals.
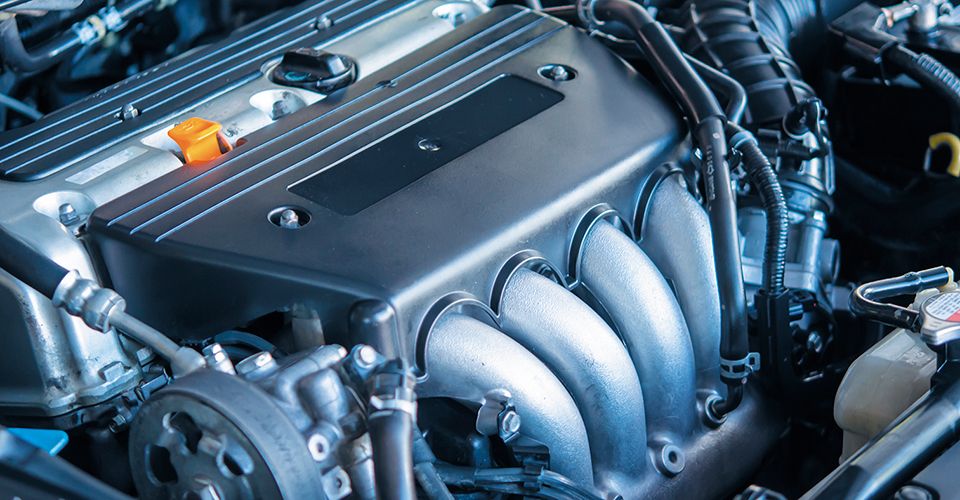
Gloves by phases
Handling with mechanical risks
Medium-level protection against cuts with a high touch need
Assembly of lightly oiled parts and heat up to 100C
Vibration
Handling of electric vibrating tools
Exterior finishings
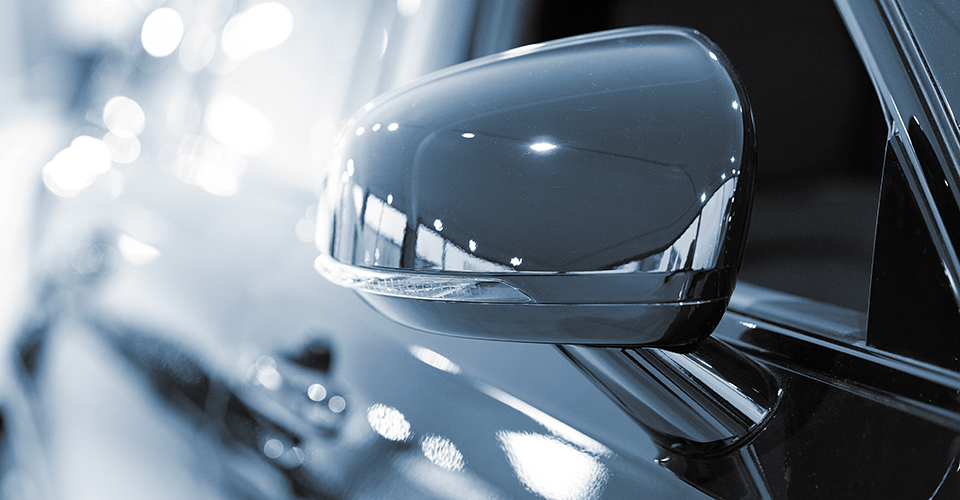
The vehicle construction process involves completing the exterior by assembling the plastic parts (bumpers and mouldings) and lighting systems (optics), glass assembly (windscreens and windows) and the fitting of tyres. In addition to these structural parts, which are installed manually, wiring is fastened in this process. A high level of touch is required for this work, so operators’ hands need protection from abrasion and possible minor cuts. Gloves must also protect installed materials without leaving traces or damage to them.
At Juba we propose a selection with over a dozen models to guarantee the care of parts and considering whether you work with electronic components or glass parts.
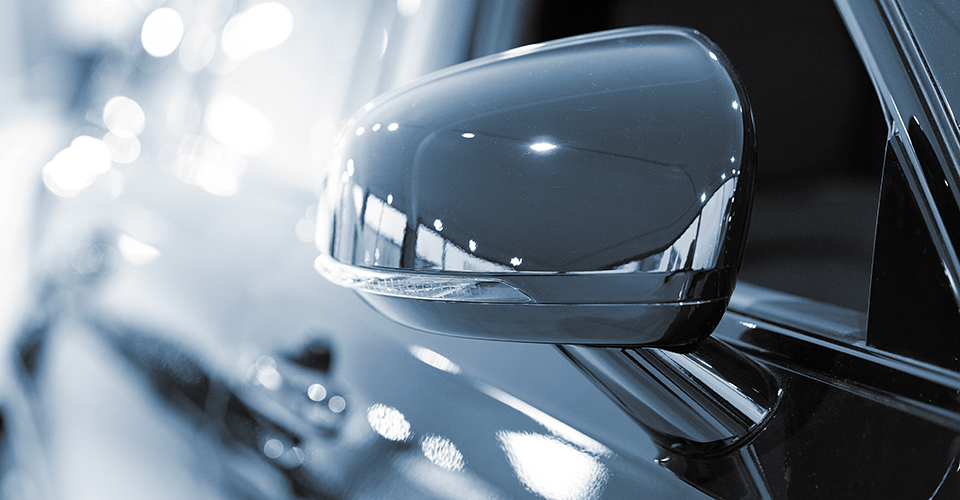
Gloves by phases
Assembly and fitting
Interior finishings
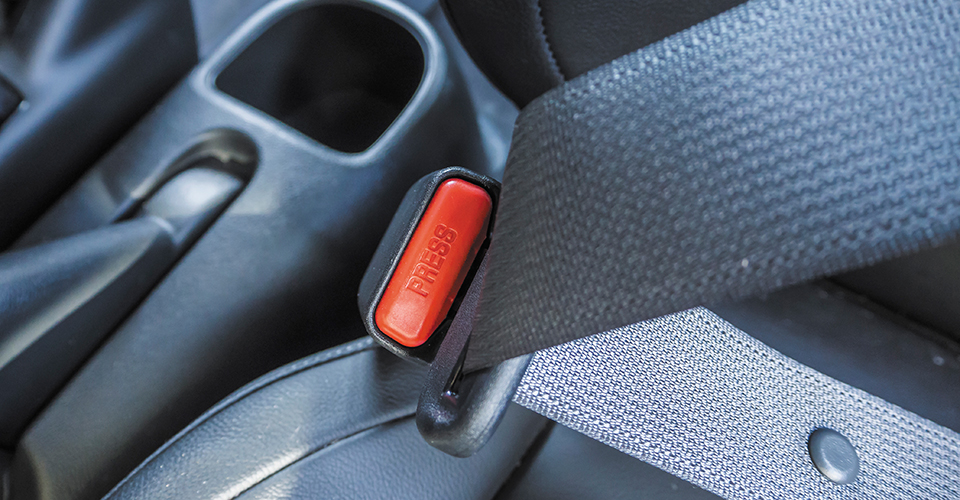
In this final phase of vehicle construction, the interior components (dashboard, safety systems, seats, upholstery and carpet) are installed and the final finishes done. A high level of touch, dexterity and grip is required in this process. Operations are performed in a clean environment, but workers must be protected from possible abrasion and minor cuts. We also need to protect the finishes from dirt and contact contamination. The finished vehicle is ready for inspection and checking.
At Juba we have selected a dozen gloves for interior assembly and vehicle care, some of which are specific to the assembly of electronic components that may require antistatic models.
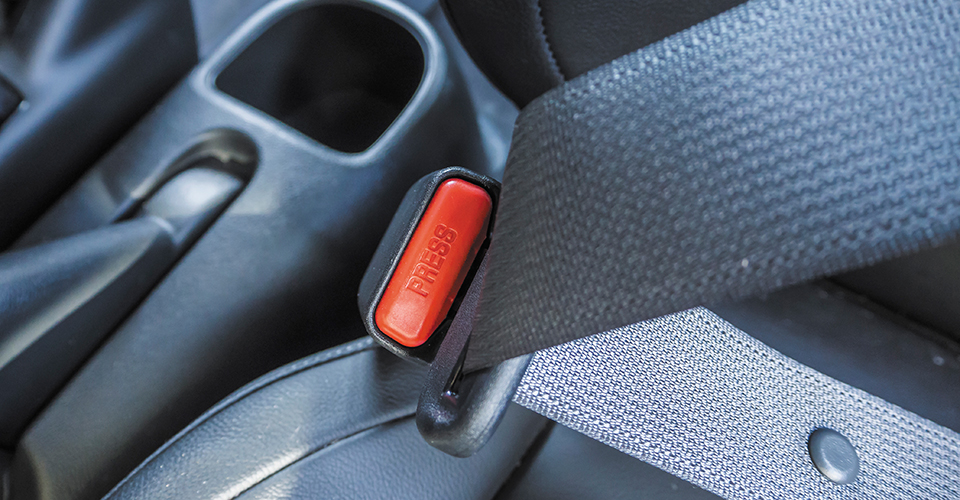
Gloves by phases
Handling with mechanical risks
Verification and inspection
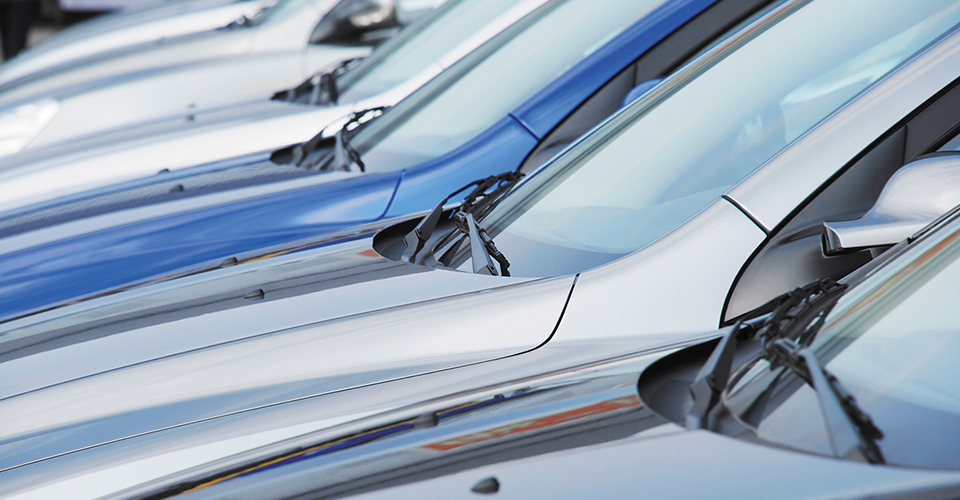
The automotive industry is highly demanding and once built, the vehicle must pass a series of checks and tests to determine its correct completion. These operations require the use of gloves that leave no trace of this work and protect the wearer from mechanical risks, depending on the task performed on the vehicle.
At Juba we offer half a dozen models that guarantee the delicate and exquisite treatment the finished product needs.