K-Rock +
Steel and metal
This industrial sector encompasses all the companies engaged in the manufacture of metal, from processing the raw material to producing a specific product or equipment. It is a broad sector covering many subsectors, all with very varied activities. Occupational risks are therefore very diverse, including those affecting workers’ upper limbs.
This industrial activity involves intensive use of the hands, which are exposed to cuts and abrasions, blows from parts, the splashing of molten metal or thermal contacts, handling and contact with chemicals…
Juba provides products for each need on the basis of the processes carried out in this sector
Casting
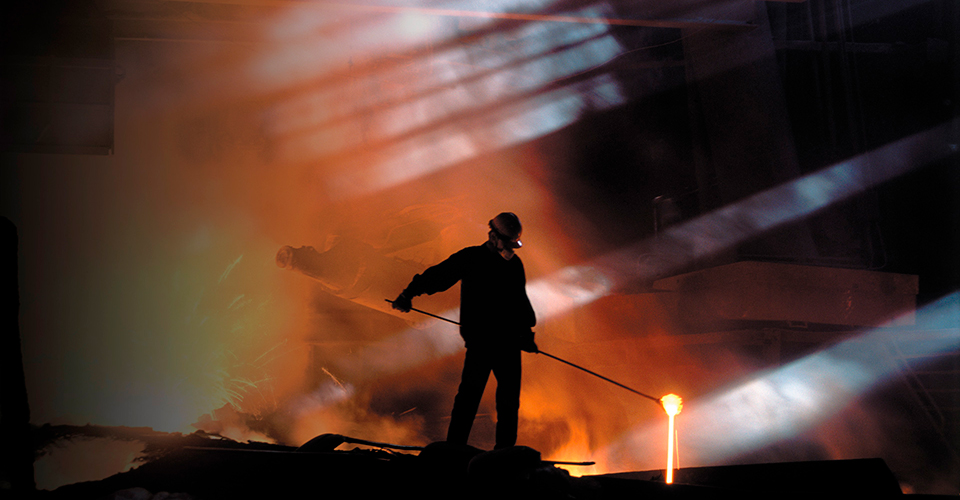
The casting process consists of pouring molten metal (liquid state) into a mould. These steps are followed to achieve this
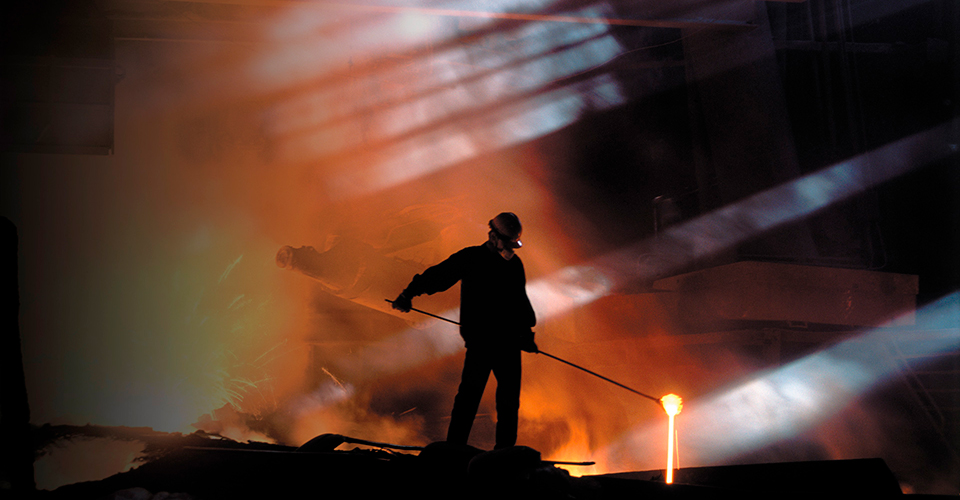
Gloves by phases
Mould manufacturing
The preparation of a mould for cast metal part manufacturing is a manual action involving mechanical risks (in preparing the case and cores) and chemical risks (in preparing the sands with the chemical additives needed for stabilisation)
Injection moulds are manufactured by the machining processes we address specifically below:
Melting: Metal injection and casting
This is the processing stage involving melting the raw material, i.e., metal, to make parts by introducing liquid metal into the mould.
Emptying
The process by which the part is removed from the case or mould, with risks associated to hand protection such as impacts, abrasion, cuts and thermal risks.
Deburring
The cast part is cleaned after it is emptied: excess metal, crusts and sprues must be removed... Hand and pneumatic tools are used in this process.
Metal forming
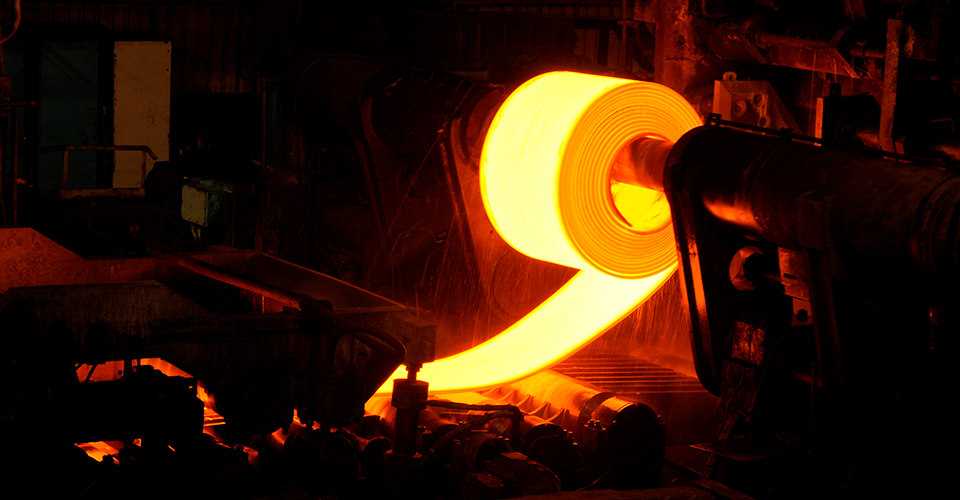
The metal must be formed in order to make a part with the desired shape. in most cases, metal parts go through two or more of the following steps to achieve this result:
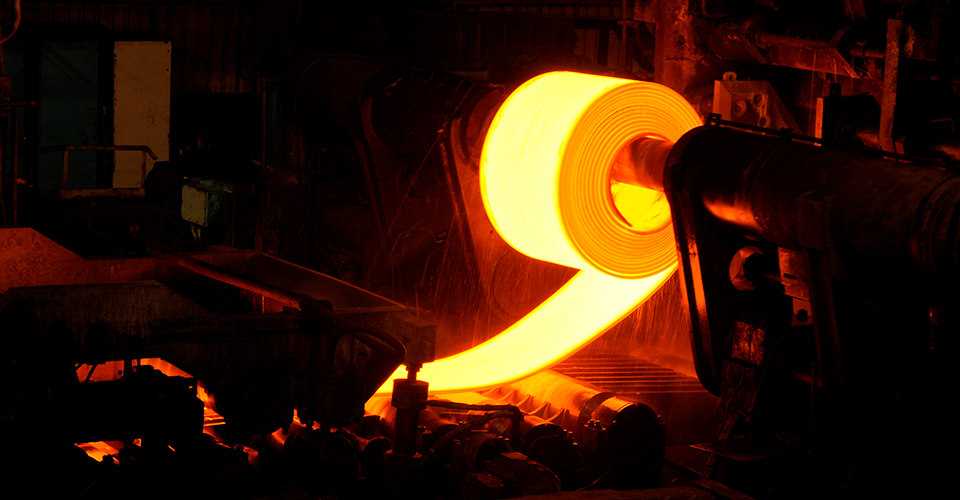
Gloves by phases
Rolling
This operation consists of transforming the metal ingots into bars or sheets with the desired format. This process can be done hot or cold. These tasks involve handling work with a risk of entrapment, cuts, burns and chemical dermatitis
Forging
This is the hot forming process with high pressure applied with presses or a hammer. The material to be processed is subjected to the maximum temperature, without reaching melting point, then formed by hammer strokes or pressure and cooled in different ways depending on the delicacy of the part. The upper limb risks associated with these tasks are entrapment, shock, vibration transmission, abrasion erosions and burns from radiant heat, contact heat or projections.
Welding
Welding operations allow metal parts to be joined by heat or pressure, or with both processes simultaneously. The most common types of welding are electric welding and oxy-acetylene welding. Oxycutting processes are metal cutting operations with gas. The risks associated with these activities are burns from splashes of incandescent material and burns from radiation or contact with the material being worked on.
Furthermore, the metal welding job must provide different finishes, requiring different types of gloves depending on the touch required and the intensity of the operation.
Machining
This is a procedure for the manufacture of parts by removing material without cutting (with a drill and by milling), by abrasion or even by the use of chemical processes.
We must also include processes with machines that deform metal: presses, folding machines, shears, bending machines, etc.
The risks associated with the upper limbs from these actions are multiple: entrapment, blows, cuts and burns from handling swarf, as well as skin conditions from contact with cutting fluids and oils.
Work with oiled parts
Risk of cutting
Surface treatments
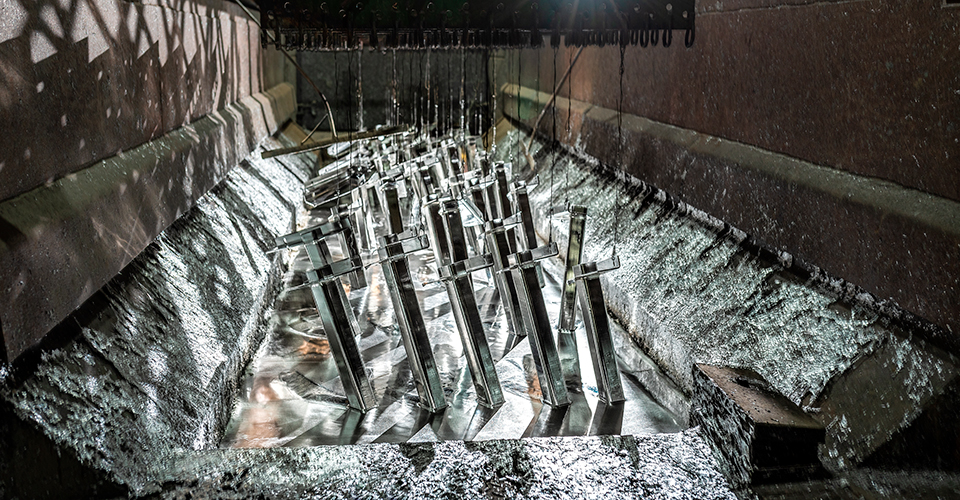
Different finishes must be applied in the manufacturing process of a metal product to prevent corrosion. Parts therefore go through various processes before coating and final image.
These processes are washing (degreasing) and drying until the final coating is applied. Washing is usually done by immersing the part in a dilute inorganic acid, hydrochloric acid or sulphuric acid; the part is then cleaned with a basic substance such as caustic soda and left to dry. After drying, the part is ready for coating with the corresponding metal bath, immersion in molten metal, anodised or lacquered.
The risks that workers’ hands are exposed to in these treatments are diverse and depend on the surface and shapes of the part: punctures, cuts, abrasions, chemical burns and chemical dermatitis.
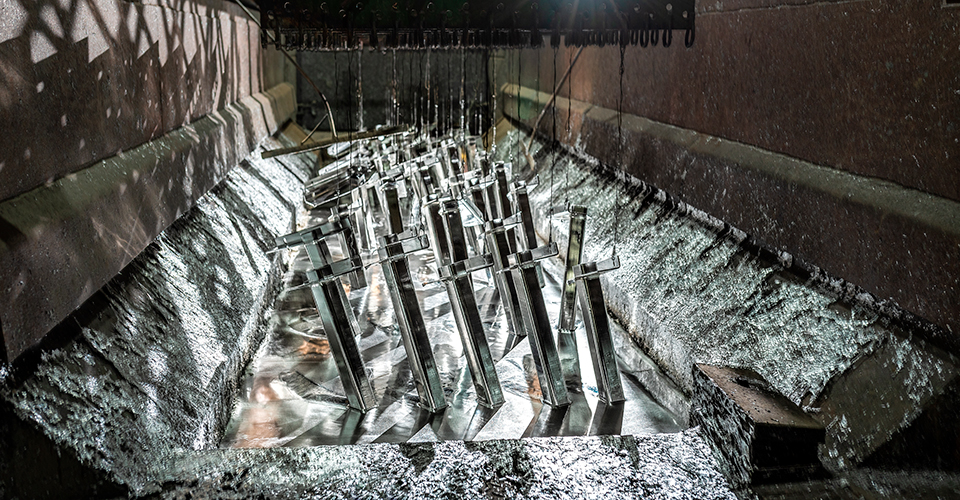
Gloves by phases
Surface treatments
Acids, inorganic bases, alcohols
Mineral oils, inorganic bases
Assembly and fitting
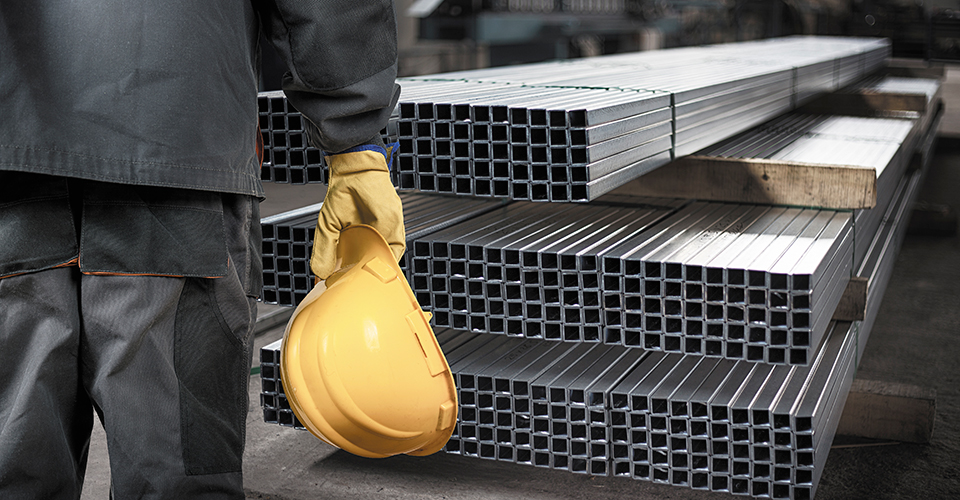
This is the final stage in the metal equipment manufacturing process, where finished or semi-finished parts are joined together to make the end product.
The risks in this phase are those inherent to assembly chains: impacts and cuts, exposure to vibrations and contact burns from hot product parts.
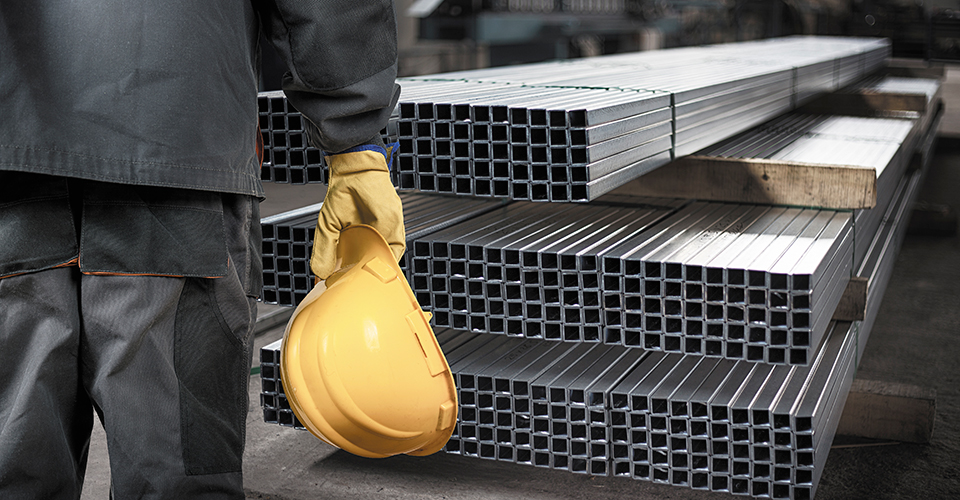
Gloves by phases
Assembly and fitting general use
Wet environment
Dry handling environment with risk of cutting
Electronic component manufacturing
Handling with risk of cutting and contact heat risk
Electric vibrating tools
Inspections
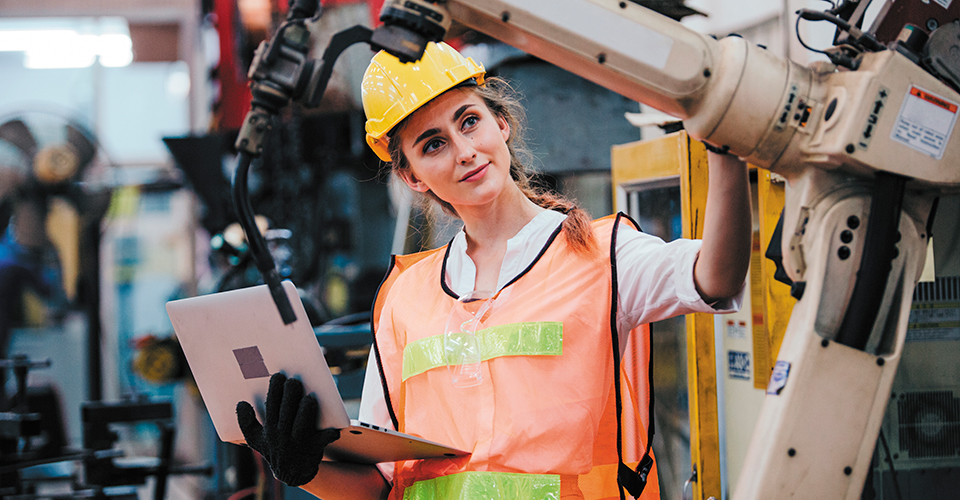
Finished product inspections require the use of gloves to protect workers and products across each type of action.
Logistics
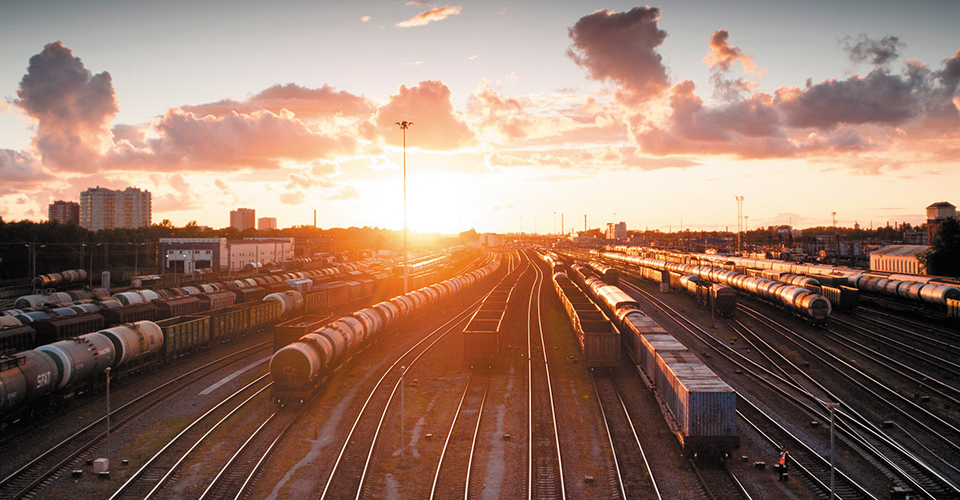
Logistics operations involve delivering components to production lines and managing the finished product by means of transportation and hoisting elements.
Gloves must protect operators from abrasion, cuts and cold, where applicable. They must also allow operations to be recorded on touch terminals.
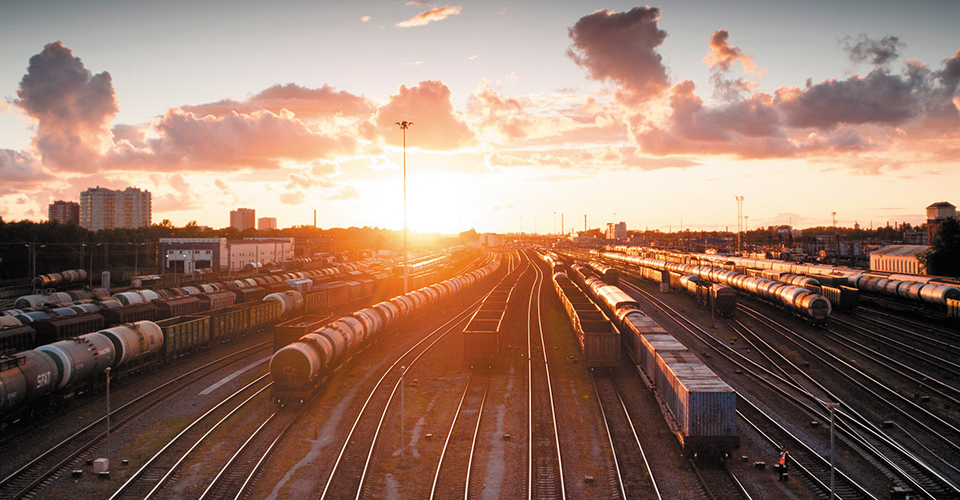
Gloves by phases
Logistics
General handling and touch devices in cold environments