K-Rock +
Ceramic industry for construction
The ceramics industry has a millenary tradition. The industrial activity that concerns us in this monograph focuses on the field of construction; we are talking about the manufacture of ceramic floor and wall tiles and decorated glazes.
The raw material is mainly of mineral origin. Clays, feldspar (such as potassium and sodium), talc, magnesite, calcite, dolomite, chromite, aluminous minerals, silicon, etc. are used.
Raw Material Preparation
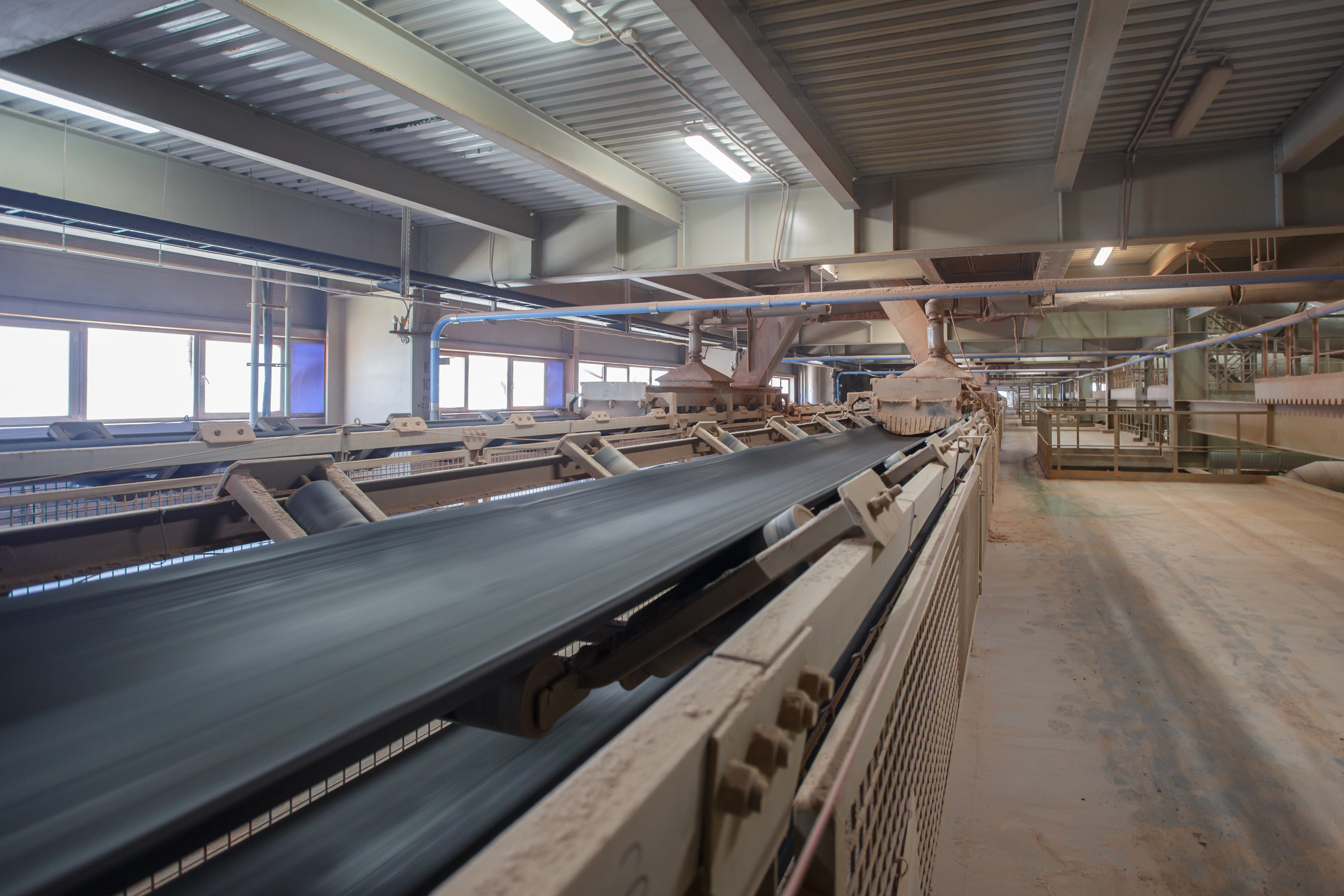
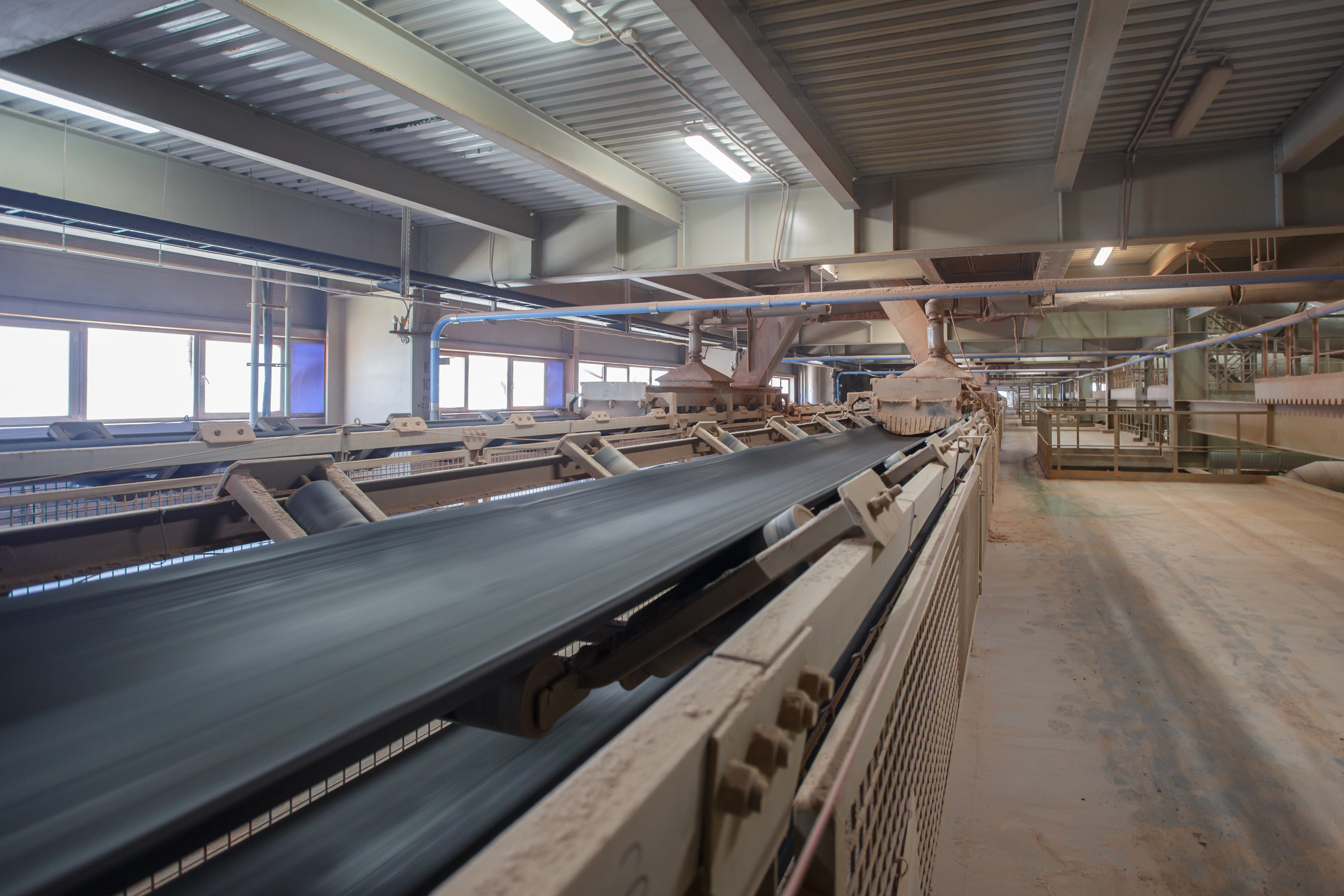
Gloves by phases
Reception and preparation
The raw materials arrive at the factory in the form of powder or sand and are stored in the mills. These are abrasive materials and require gloves with good abrasion resistance, as well as good abrasion resistance and comfort. Although most of these processes are mechanised, workers have to organise and plan the reception of materials and the preparation of quantities for further processing and grinding.
Grinding
Grinding is the process in which the material is pulverised to create a homogeneous mixture, producing a large amount of powder at this stage. Chemicals and water are added until the slurry is created. At this stage, the operator must protect his hands from moisture and dust.
Atomisation
The slip is exposed to high temperatures which dry and pulverise the material so that it can be treated. The large atomisation tanks handle large quantities of material and the processes are mostly mechanised. At this stage workers have contact with water and dust, as movement between tanks is mechanised. Some waterproofing and gloves to protect against dust abrasion are required.
Manufacture of the Part
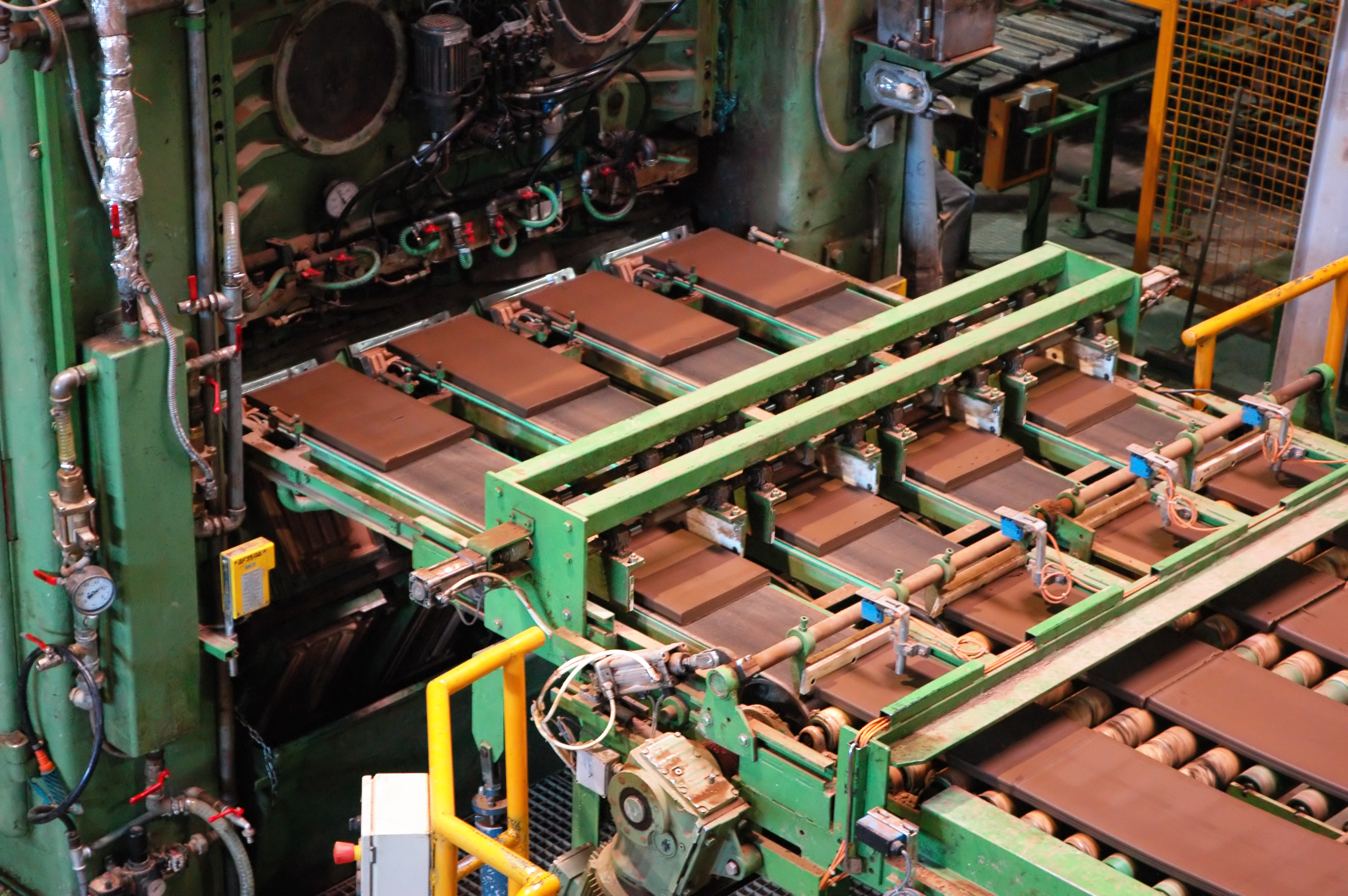
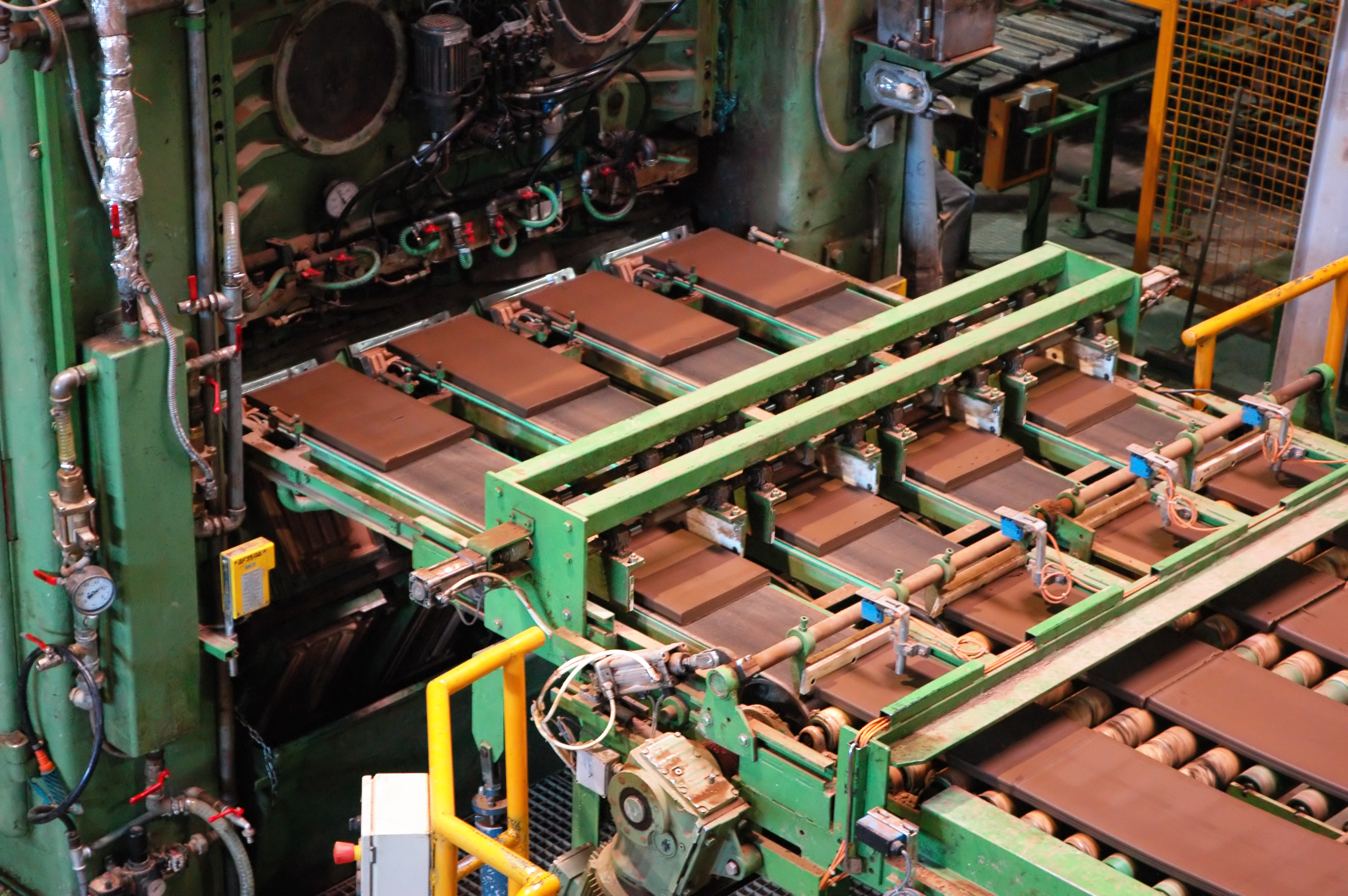
Gloves by phases
Drying
The pressed part must be dried to remove moisture. The main risk to workers is moderate contact heat, as there is handling of parts when transferring them from the press to drying. There may be a risk of cutting when parts break. Operators mainly supervise the process.
Decoration of the piece: enamelling, screen printing and glazing
Once the piece is formed and dried, it is time to decorate it. The decoration techniques are enamelling, screen printing and glazing. Chemical products are used for these. In addition, the glazing process forms a crystallised layer on the surface which is very sharp in case of breakage. Hand protection at this stage involves resistance to chemicals and the handling of very sharp workpieces with a high level of grip
Firing
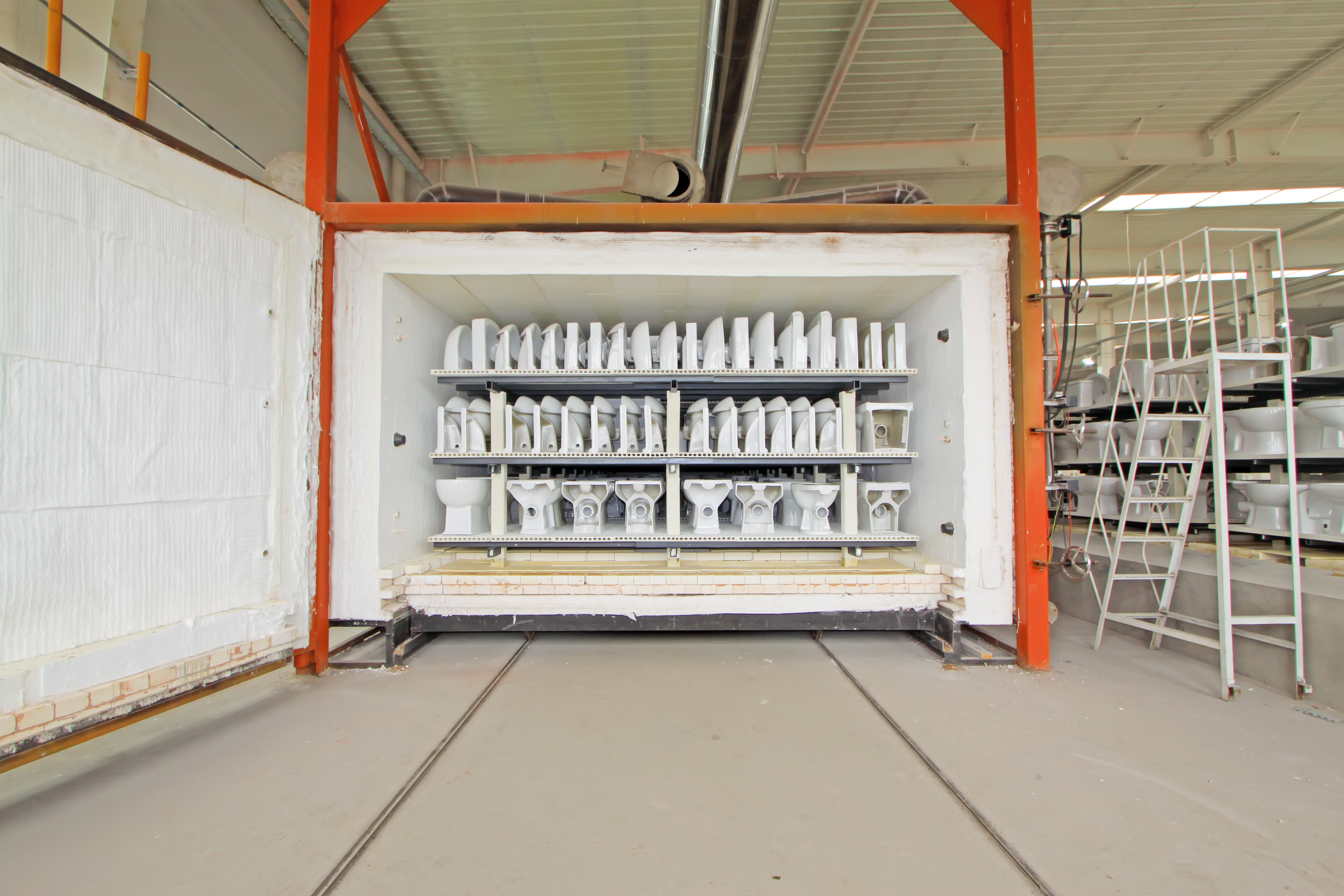
The last firing consists of baking the piece at high temperatures, at which point it acquires a glazed and glazed appearance. The thermal risk is moderate, as the pieces come out of the oven at moderate temperatures.
However, when incidents occur in the baking process, aluminised gloves are necessary for optimum thermal protection.
Decoration and polishing
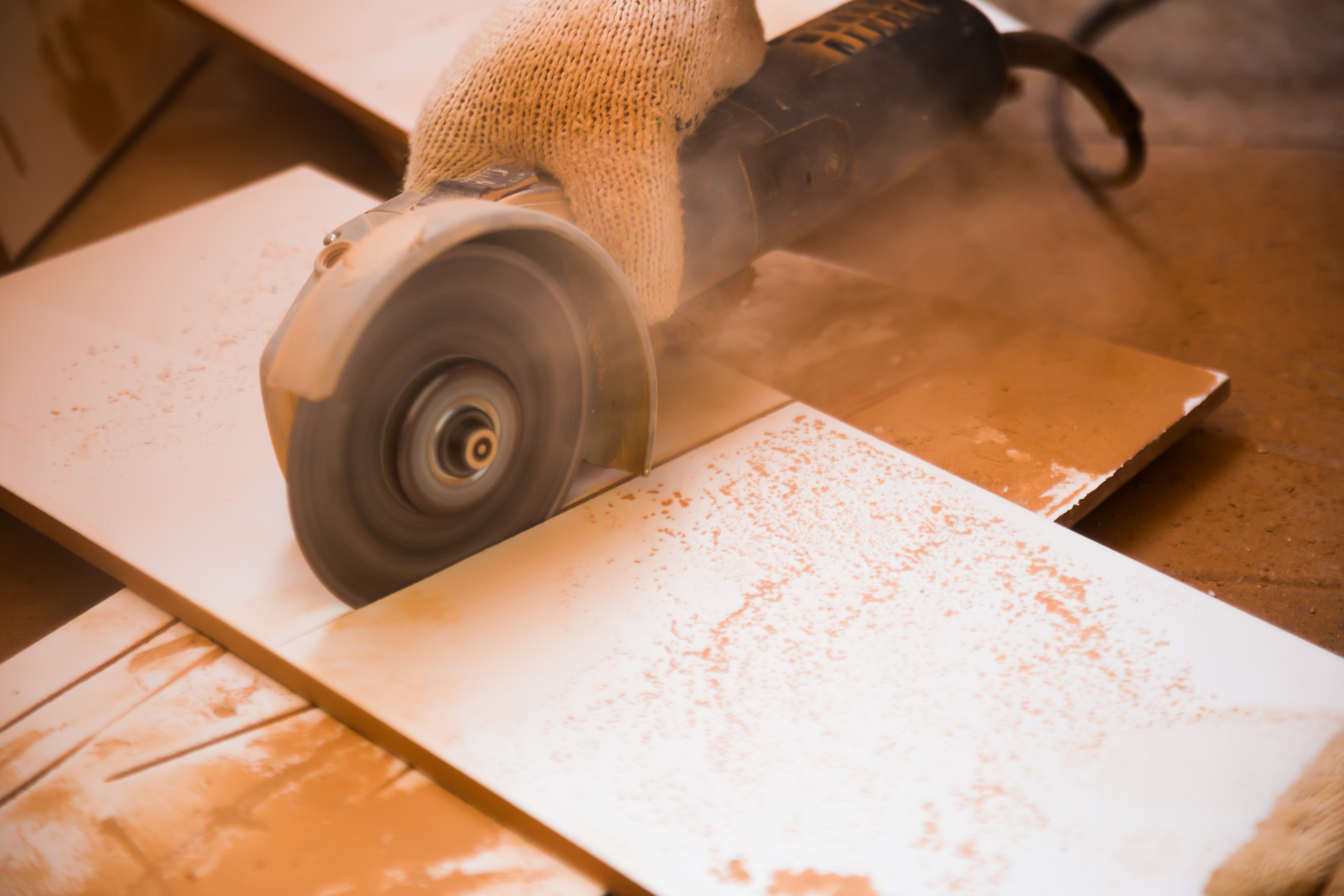
The fired piece may go through a further decoration phase, depending on the final result required, in which chemicals are again applied for ornamentation.
Ceramics can have very sharp edges. Workpieces are handled for polishing or grinding, which requires the use of cut-resistant protection.
Classification/Inspection/Packaging
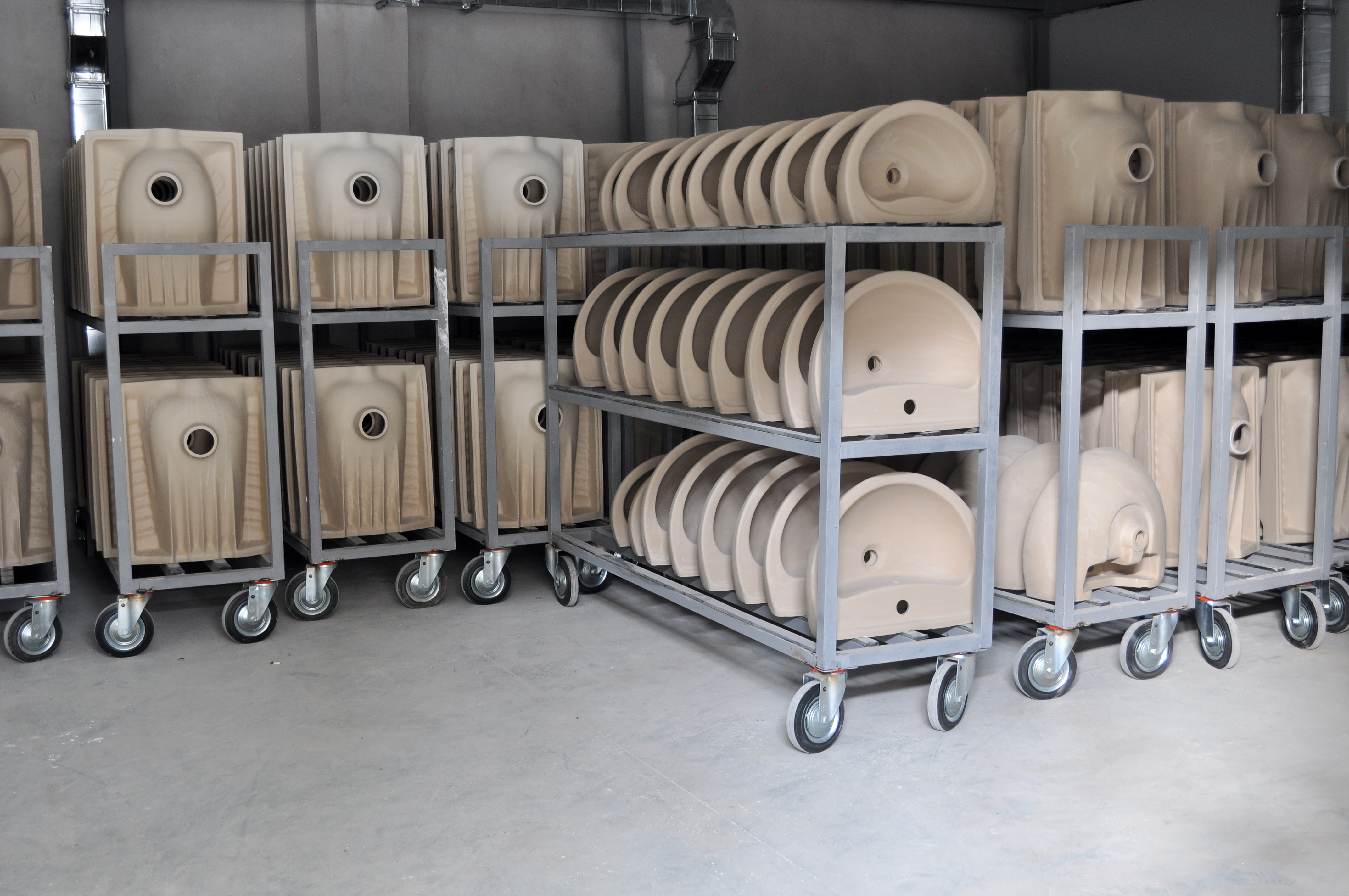
The parts are separated and sorted, packaged and prepared for distribution. Warehouse work in this industry involves, in addition to the handling typical of a warehouse, a high risk of cutting when the product breaks. It should be borne in mind that ceramics is a fragile product, so breakage is a common risk. In addition, other applications for handling palletised goods require general-purpose gloves such as polyurethane, due to their good grip.
Testing Laboratory
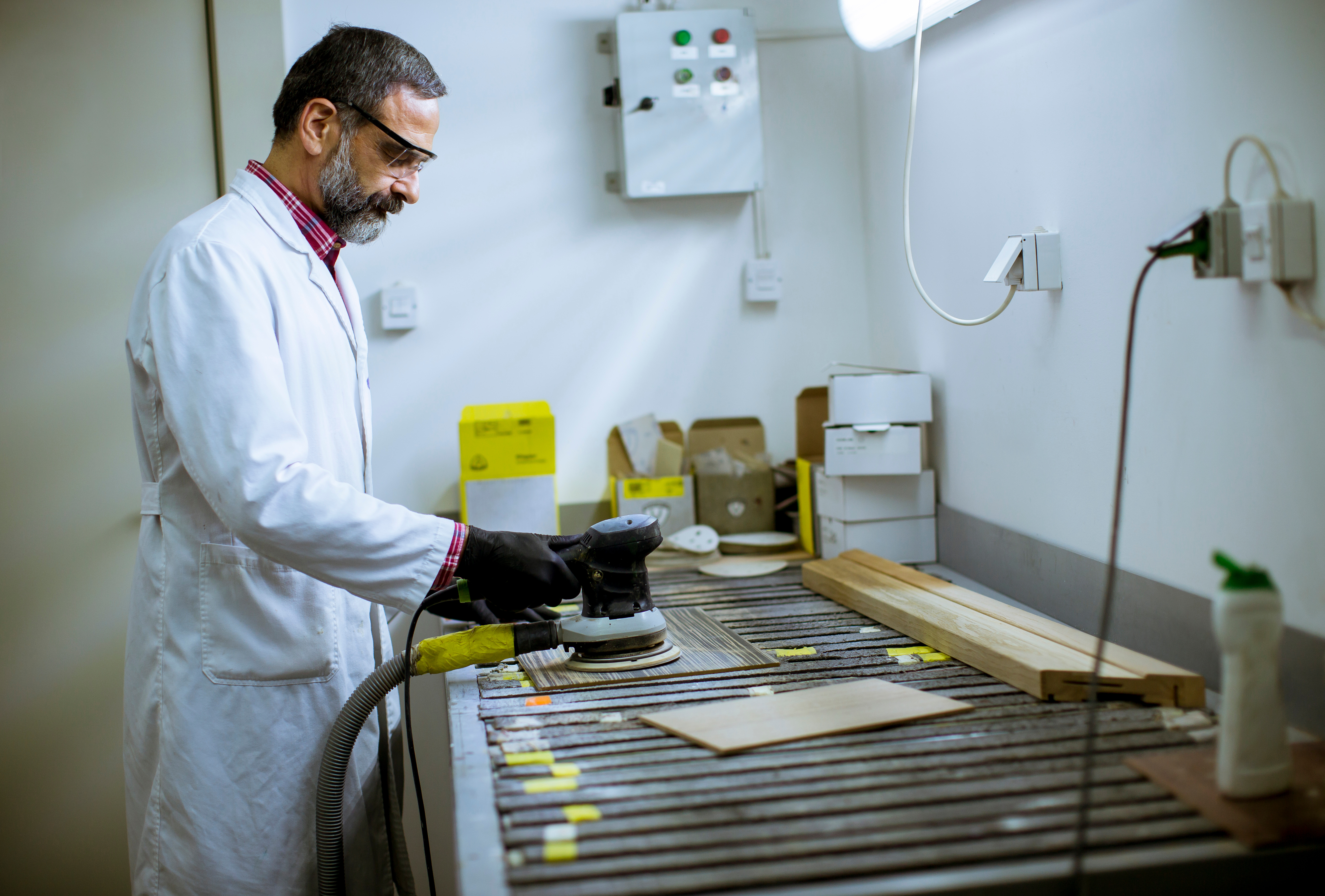
The ceramics laboratory carries out tests both at the beginning of the process, controlling the raw material, and during the following production processes.