Glove standard
Regulation: Standard issued by the organs of the European Union directly applicable in the Member States, without the need for transposition. Published March 31, 2016 in the DOUE comes into force on April 21, 2018. From April 21, 2019, distributors will be able to introduce EPIS into the market in accordance with the new Regulation 2016/425.
Main changes to the new EU regulation 2016/425
- It goes from being a Directive to a mandatory Regulation in all EU countries.
- The CE Declaration of Conformity will be named the EU Declaration of Conformity, and the standards to which it refers will be cited with the year of update or revision: EN388: 2016 or ENISO374: 2016.
- CE Certificates will be named as EU Certificates.
- The Prospectus must include a link where you can download the EU Declaration of Conformity.
- The manufacturer agrees to establish traceability on its EPIS.
- An expiration of 5 years is imposed on the EU Type Examination Certificates that will require the recertification of all EPIS.
- EPIS designed to protect against chainsaw portable chainsaw cuts become Category III EPIS.

Includes the following minimum risks: (superficial mechanical injuries, contact with weakly acting cleaning materials or extensive contact with water, contact with hot surfaces not exceeding 50ºC., eye injuries caused by sunlight non extreme atmospheric conditions. Internal production control (Module A) is carried out in accordance with Annex IV.

It includes risks other than those listed in categories I and III. EU type examination (Module B) under Annex V, followed by conformity to the type based on internal production control (Module C) under Annex VI

Exclusively includes risks that might incur very serious consequences, such as death or irreversible damage to health, in relation to the following: (substances and mixtures dangerous to health, atmospheres lacking oxygen, harmful biological agents, ionizing radiation, atmospheres with high temperatures whose effects are comparable to those of an air temperature of at least 100ºC, low temperature environments whose effects are comparable to those of an air temperature of -50ºC or less, falls from height, electric shocks and live work , drowning, cuts by hand-operated chain saws, high-pressure jets, gunshot or stab wounds, harmful noises).
EU type examination (Module B) according to Annex V and any of the following options:
- Type conformity based on internal production control plus supervised product control at random intervals (Module C2) according to Annex VII.
- Conformity with the type based on the quality assurance of the production process (Module D) under Annex VIII.
The standard defines general requirements:Glove design and construction
- Resistance of glove materials to water penetration
- Safety: pH between 3.5 and 9.5 according to EN ISO 4045 / EN 1413, chromium VI content less than 3.0 mg / kg according to EN ISO 17075: 2007 for leather gloves and extractable proteins according to EN 455-3 for natural rubber gloves.
- Cleaning
- Electrostatic properties.
The standard defines comfort and effectiveness:
- Sizes.
- Desterity.
- Transmission and absorption of water vapor.
DIMENSIONS OF THE HAND |
|||
---|---|---|---|
SIZES |
CIRCUMFERENCE |
LENGTH |
GLOVE DIMENSION |
6 |
152 |
160 |
220 |
7 |
178 |
171 |
230 |
8 |
203 |
182 |
240 |
9 |
229 |
192 |
250 |
10 |
254 |
204 |
260 |
11 |
279 |
215 |
270 |
Skill:
- Nested table.
HAND SKILL |
|
---|---|
PROTECTION LEVEL |
DIAMETER OF THE SMALLEST ROD THAT MEETS THE TEST CONDITIONS (MM) |
1 |
11,0 |
2 |
9,5 |
3 |
8,0 |
4 |
6,5 |
5 |
5,0 |
It includes mittens and kitchen mitts and potholders in the object and field of application.
Harmless
In addition to the above requirements, a series of recommendations regarding the substances
in the gloves is introduced:
- Any metal component which may come into prolonged contact with the skin (e.g. tacks, fittings) must have a nickel release of less than 0.5 μg/cm2 per week.
- Azo dyes that release carcinogenic amines should not be detectable.
- Dimethylformamide (DMFa) in gloves containing PUs should not exceed 1000 mg/kg.
- Polycyclic aromatic hydrocarbons (PAHs) shall not exceed 1 mg/kg for rubber or plastic materials intended to come into direct contact with the skin.
The performance levels for gloves that can be washed will be the lowest obtained after the cleaning process.
In multi-layer gloves, the integrity of the layers in the finger area must be ensured.
The gloves should allow the transmission of water vapour whenever possible.
- Leather gloves - Transmission of water vapour > 5 mg/(cm2·h).
- Textile gloves - Water vapour resistance ≤ 30 m2·Pa/W.
The requirements for electrostatic properties must be checked in accordance with the specific standard for antistatic gloves EN16350. For protective gloves with electrostatic dissipation, each individual measure must comply with the requirement: Vertical Resistance RV< 1.0 X 108Ω (Ohm) and is accompanied by a new logo to be indicated on the gloves.
The manufacturing date or any other means ensuring traceability of the manufacturing series must be indicated. When an obsolescence date has to be entered, it should be done by adding the hourglass pictogram.
Hand Sizes: A new size table is introduced, extending the range from 4 to 13.
HAND DIMENSIONS |
||
---|---|---|
SIZES |
CIRCUMFERENCE |
LENGHT |
4 |
101 |
< 160 |
5 |
127 |
< 160 |
6 |
152 |
160 |
7 |
178 |
171 |
8 |
203 |
182 |
9 |
229 |
192 |
10 |
254 |
204 |
11 |
279 |
215 |
12 |
304 |
> 215 |
13 |
329 |
> 215 |
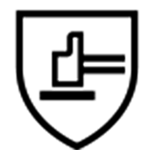
EN388:2016 Protective gloves against mechanical risks.
The EN388: 2003 standard is renamed EN388: 2016, the year of its revision. The reason for the modification is given by the discrepancies in the results between laboratories in the knife cut test, COUP TEST. Materials with high levels of cut produce a dulling effect on the circular blades, which undermines the result.
The new regulation was published in November 2016 and the previous one is from the year 2003. During these 13 years, there has been a great innovation in the materials for the manufacture of cutting gloves, they have forced to introduce changes in the tests to be able to measure with more rigorous levels of protection.
A - Abrasion resistance (X, 0, 1, 2, 3, 4)
B - Blade Cut Resistance (X, 0, 1, 2, 3, 4, 5)
C - Tear resistance (X, 0, 1, 2, 3, 4)
D - Puncture resistance (X, 0, 1, 2, 3, 4)
E - Cutting by sharp objects ISO 13997 (A, B, C, D, E, F)
F - Impact test complies / does not comply (It is optional. If it complies, put P)
EN388:2016 PERFORMANCE LEVELS |
1 |
2 |
3 |
4 |
5 |
---|---|---|---|---|---|
6.1 Abrasion resistance (Cycles) |
100 |
500 |
2000 |
8000 |
- |
6.2 Blade cut resistance (Index) |
1,2 |
2,5 |
5 |
10 |
20 |
6.4 Tear resistance (Newtons) |
10 |
25 |
50 |
75 |
- |
6.5 Puncture resistance (Newtons) |
20 |
60 |
100 |
150 |
- |
ENISO13997:1999 PERFORMANCE LEVELS |
A |
B |
C |
D |
E |
F |
---|---|---|---|---|---|---|
6.3 TDM: Cut resistance (Newtons) |
2 |
5 |
10 |
15 |
22 |
30 |
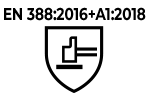
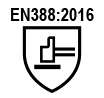
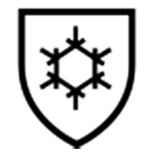
Levels vs temperature of glove use
If the convective cold is level 0 - This glove can be used up to a temperature of 0ºC
If the convective cold is level 1 - This glove can be used up to a temperature of -10ºC
If the convective cold is level 2 - This glove can be used up to a temperature -20ºC
If the convective cold is level 3 - This glove can be used up to a temperature of -30ºC
If the convective cold is level 4 - This glove can be used up to a temperature of -40ºC
Gloves on both hands must meet the requirements below:
PERFORMANCE LEVEL |
|
1 |
2 |
3 |
4 |
---|---|---|---|---|---|
A Convective cold resistance* |
ITR thermal insulation in m² ºC/W |
0,10 ≤ ITR ≤ 0,15 |
0,15 ≤ ITR ≤ 0,22 |
0,22 ≤ ITR ≤ 0,30 |
0,30 ≤ ITR |
B Contact cold resistance |
Thermal resistance R in m² C/W |
0,025 ≤ R ≤ 0,050 |
0,050 ≤ R ≤ 0,100 |
0,100 ≤ R ≤ 0,150 |
0,150 ≤ R |
C Water impermeability |
Waterproof for at least 5 minutes |
Pass |
|
|
|
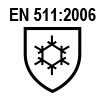

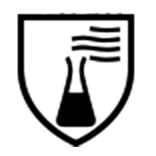
The EN374: 2003 standard is renamed ENISO374: 2016. The purpose of this standard is to classify gloves according to their behavior when exposed to chemical substances.
They are divided into the following parts:
EN ISO 374-1:2016 - Terminology and performance requirements for chemical risks.
EN 374-2:2014 - Determination of resistance to penetration.
EN 16523-1:2015 + A1:2018 - Permeation by liquid chemicals under continuous contact conditions.
EN ISO 374-4:2019 - Determination of resistance to chemical degradation.
EN ISO 374-5:2016 - Terminology and requirements demanded for risks of microorganisms.
Gloves classification according to ENISO374-1: 2016
Gloves are divided into three types:
TYPE A
Step time ≥ 30 min for at least 6 products
TYPE B
Step time ≥ 30 min for at least 3 products
TYPE C
Step time ≥ 10 min for at least 1 products
LETTER |
CHEMICAL SUBSTANCE |
CAS NUMBER |
CLASS |
---|---|---|---|
A |
Methanol |
67-56-1 |
Primary alcohol |
B |
Acetone |
67-64-1 |
Cetone |
C |
Acetonitrile |
75-05-8 |
Nitrile compound |
D |
Dichloromethane |
75-09-2 |
Chlorine hydrocarbon |
E |
Carbon disulfide |
75-15-0 |
Sulphate organic compound |
F |
Toluene |
108-88-3 |
Aromatic hydrocarbon |
G |
Diethylamine |
109-89-7 |
Amine |
H |
Tetrahydrofuran |
109-99-9 |
Heterocyclic ether |
I |
Ethyl acetate |
141-78-6 |
Ester |
J |
n-heptane |
142-85-5 |
Saturated hydrocarbon |
K |
Sodium Hydroxide 40% |
1310-73-2 |
Inorganic alkaline |
L |
Sulphuric acid 96% |
7664-93-9 |
Inorganic, oxidising mineral acid |
M |
Nitric acid 65% |
7697-37-2 |
Inorganic, oxidising mineral acid |
N |
Acetic acid 99% |
64-19-7 |
Organic acid |
O |
Ammonia Hydroxide 25% |
1332-21-6 |
Organic Alkaline |
P |
Hydrogen peroxide 30% |
7722-84-1 |
Peroxide |
S |
Hydrofluoric acid 40% |
7664-39-3 |
Mineral organic acid |
T |
Formaldehyde 37% |
50-00-0 |
Aldehyde |
Levels of resistance to permeability
TAVERAGE PENETRATION TIME |
PERFORMANCE LEVELS |
AVERAGE PENETRATION TIME |
PERFORMANCE LEVELS |
---|---|---|---|
> 10 |
Class 1 |
> 120 |
Class 4 |
> 30 |
Class 2 |
> 240 |
Class 5 |
> 60 |
Class 3 |
> 480 |
Class 6 |
Gloves classification according to EN374-2:2014
It is the advance of chemical products through the material, seams of the glove at a non-molecular level. Air leak test: the glove is inflated with air and immersed in water. The appearance of air bubbles is controlled within 30 '. Water leak test: the glove is filled with water and the appearance of water droplets is controlled. If these tests are positive, the pictogram will be put on.
Gloves classification according to EN374-4: 2013
Detriment to some of the glove's properties due to contact with a chemical. Eg: discoloration, hardening, softening, etc.Permeation test EN 16523-1. It is the advancement of chemicals at the molecular level. The resistance of the glove material to permeation by a chemical is determined by measuring the time it passes through the material.
Modification of the ENISO374-5: 2016 standard
When the glove passes the test described for virus protection, the word “virus” will appear under the pictogram. If nothing appeared, protection would only be assured against bacteria.
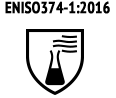
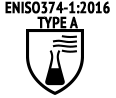
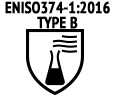
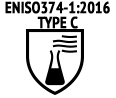
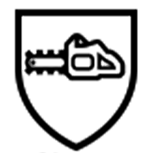
EN 381-7:1999 – Chainsaw risks
The minimum levels required for the EN388 standard are as follows:
Abrasion resistance 2
Cut resistance 1
Tear resistance 2
Puncture resistance 2
Protection against cutting by chain saws:
CLASS |
SPEED |
---|---|
0 |
16 m/s |
1 |
20 m/s |
2 |
24 m/s |
3 |
28 m/s |
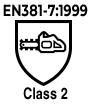

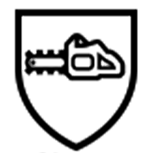
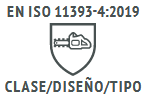
The minimum levels required for the EN388 standard are as follows:
Abrasion resistance 2
Cut resistance 1
Tear resistance 2
Puncture resistance 2
Protection against chainsaw cutting should be evaluated with the following chainsaw speeds.
CLASS |
SPEEDS |
---|---|
0 |
16 m/s |
1 |
20 m/s |
2 |
24 m/s |
3 |
28 m/s |
Classification by type
TYPE1 Protection against chainsaw cutting in both right and left hands.
TYPE2 Chain cut protection only on left hand. The right hand has no cut protection.
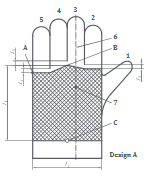
Design A
Only applicable for gloves with cut protection in the metacarpal area, but not on fingers or thumb.
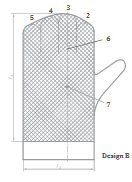
Design B
Applicable to gloves and 3-finger mitts incorporating, in addition to design A protection, the back of the fingers (except thumb).
Main changes with previous standard:
Requirements that in EN381-7 were optional, cleaning, dexterity and water vapour permeation and absorption, become mandatory. It becomes mandatory to measure dexterity by means of a grip test essay on a bar with a pressure sensor.
Water vapour permeation is mandatory for coated gloves.In the cutting test, the changes are: Pre-treatment – cleaning according to the Manufacturer’s instructions. The number of cuts significantly increases the number of cuts and the areas. All of them are mandatory.
TYPE |
DESIGN |
|
---|---|---|
A |
B |
|
1 |
Position 1: two in left hand |
Posición 5: two in left hand |
2 |
Posición 1: two in left hand |
Posición 1: two in left hand |
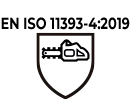
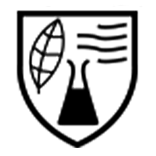
Minimum requirements for workers in contact with pesticides.
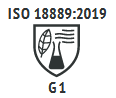
- Chemical protection all over the hand.
- Relatively low potential risk.
- Handling of diluted pesticides.
- No mechanical hazards.
- Disposable: minimum length 240 mm.
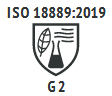
- Chemical protection all over the hand. Increased potential risk
- More protection than the G1.
- Handling of concentrated or diluted pesticides.
- Minimum length 290 mm.
- Minimum mechanical protection: abrasion - level 2, cutting - level 1 or letter A and perforation - level 1.
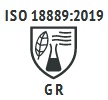
- Partial hand protection (fingers and palm):
- Minimum mechanical protection for handling tasks: abrasion-level 2, cutting – level 1 or A, tearing – level 1 and perforation – level 1.
- For users in contact with partially dried or dried pesticide residues existing on the plant after applying the pesticide.
- They cannot be used to replace the G1 or G2 that protect the whole hand.
- A breathable material on the back of the glove enhances comfort.
SUB-CLAUSE |
ACTION |
STANDARD;CLAUSE |
REQUIREMENTS |
||
---|---|---|---|---|---|
G1 |
G2 |
GR |
|||
4.1 |
General requirements |
ISO 21420 |
Compliant |
Compliant |
Compliant |
4.2.1 |
Penetration Test |
EN 374-2:2014, 7.2 y 7.3 |
Pass |
Pass |
|
4.2.2.1 |
Resistance to permeation |
ISO 374-1 |
≥TypeC |
≥Type B |
≥Level2 with chemical K |
4.2.2.2 |
Resistance to permeation |
ISO 19918 |
≤ 10 ug/cm2 |
≤ 1 ug/cm2 |
≤ 1 ug/cm2 |
4.2.3.1 |
Glove length |
|
Compliant |
Compliant |
|
4.2.3.2 |
Coated area |
|
|
|
Compliant |
4.2.4 |
Mechanical requirements |
ISO 23388:2018, 6.1 |
|
≥ Level 2 |
≥ Level 2 |
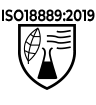
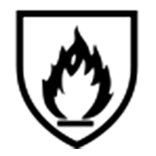
A - Flame behaviour
The material should comply with the requirements in the table. In addition, the material should not drip or melt. The seams should not open up after 15 seconds ignition time.
SERVICE PROVISION LEVEL |
POST-INFLAMMATION TIME |
POST-INCANDESCENCE TIME |
---|---|---|
1 |
≤ 20 |
No requirement |
2 |
≤ 10 |
≤ 120 |
3 |
≤ 3 |
≤ 25 |
4 |
≤ 2 |
≤ 5 |
B - Heat per contact:
The material should comply with:
SERVICE PROVISION LEVEL |
CONTACT TEMPERATURE( |
THRESHOLD TIME (s) |
---|---|---|
1 |
100 |
≥ 15 |
2 |
250 |
≥ 15 |
3 |
350 |
≥ 15 |
4 |
500 |
≥ 15 |
C - Convective heat
The material should comply with:
SERVICE PROVISION LEVEL |
HTI HEAT TRANSFER INDEX |
---|---|
1 |
≥ 4 |
2 |
≥ 7 |
3 |
≥ 10 |
4 |
≥ 18 |
D - Radiating heat
The material should comply with:
SERVICE PROVISION LEVEL |
HEAT TRANSFER INDEX T3 |
---|---|
1 |
≥ 7 |
2 |
≥ 20 |
3 |
≥ 50 |
4 |
≥ 95 |
E - Small splashes
The number of droplets necessary to produce a 40ºC rise in temperature should meet requirements in the table:
SERVICE PROVISION LEVEL |
NUMBER OF DROPLETS |
---|---|
1 |
≥ 10 |
2 |
≥ 15 |
3 |
≥ 25 |
4 |
≥ 35 |
F - Large splashes
The PVC film that simulates the skin will not be smoothed or its surface roughness changed in any other way, with any of the quantities of iron used:
SERVICE PROVISION LEVEL |
MOLTEN IRON (g) |
---|---|
1 |
30 |
2 |
60 |
3 |
120 |
4 |
200 |
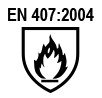

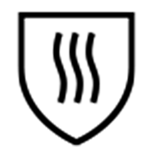
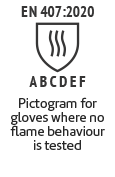
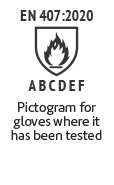
Ratified by the Spanish Standardisation Association in June 2020.
Main changes:
- Extension of the scope of the standard to domestic use: oven mitts/gloves.
- Gloves that reach a level 3 or 4 of any thermal property must reach at least a level 3 in flame propagation. Otherwise, the maximum level that may be reached in the relevant thermal property shall be level 2.
- Propagation limited to flame: prohibition of hole formation. Reduction of maximum post-combustion time for level 1. Change in ignition timing.
- Heat by contact. Obligation to test any material coming in contact with heat.
- Tear resistance. This trial is included.
- Convective heat. The test is performed without reinforcement.
- New pictogram, for gloves without flame protection.
- A minimum length is introduced when resistance against small molten metal splashes is present.
- After heat resistance tests, the samples must not suffer signs of melting or holes.
MINIMUM LENGTH OF THE TESTED GLOVES FOR E OR F |
|
---|---|
SIZE |
LENGTH |
5 |
290 |
6 |
300 |
7 |
310 |
8 |
320 |
9 |
330 |
10 |
340 |
11 |
350 |
12 |
360 |
13 |
370 |
A - Flame Behaviour
Changes in method and table. To perform the test, the ignition time now goes from 15 to 10" and the post-ignition time for level 1 goes from 20 to 15".
LEVEL OF PREFORMANCE |
POST-INFLAMMATION TIME |
POST IGNITION TIME |
---|---|---|
1 |
≤ 15 |
Not required |
2 |
≤ 10 |
≤ 120 |
3 |
≤ 3 |
≤ 25 |
4 |
≤ 2 |
≤ 5 |
B - Heat by contact
Changes in the test method. In EN407:2004 only the palm is tested, whereas with EN407:2020 any other point that may come into contact is tested.
- Contact temperature
- Threshold time (S)
LEVEL OF PERFORMANCE |
CONTACT TEMPERATURE |
THRESHOLD TIME (S |
---|---|---|
1 |
100 |
≥ 15 |
2 |
250 |
≥ 15 |
3 |
350 |
≥ 15 |
4 |
500 |
≥ 15 |
C - Convective heat
Changes in the test method. From EN373 to ENISO9185:2007
LEVEL OF PERFORMANCE |
HTI HEAT TRANSFER RATE |
---|---|
1 |
≥ 4 |
2 |
≥ 7 |
3 |
≥ 10 |
4 |
≥ 18 |
D - Radiant heat
There are no modifications. Internal layers must not show signs of melting or show holes.
LEVEL OF PERFORMANCE |
HEAT TRANSFER RATE T3 |
---|---|
1 |
≥ 7 |
2 |
≥ 20 |
3 |
≥ 50 |
4 |
≥ 95 |
E - Small splashes
There are no modifications. Internal and external layers may not be melted or pierced.
LEVEL OF PERFORMANCE |
NUMBER OF DROPS |
---|---|
1 |
≥ 5 |
2 |
≥ 15 |
3 |
≥ 25 |
4 |
≥ 35 |
F - Large splashes
Changes in the test method.
LEVEL OF PERFORMANCE |
CAST IRON (G) |
---|---|
1 |
30 |
2 |
60 |
3 |
120 |
4 |
300 |
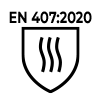
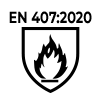
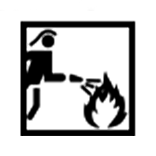
Minimum levels are required for standards EN388 and EN407 and minimum lengths.
MINIMUM LENGTH | |
---|---|
SIZE |
MINIMUM LENGTH |
6 |
260 mm |
7 |
270 mm |
8 |
280 mm |
9 |
290 mm |
10 |
305 mm |
11 |
315 mm |
MINIMUM REQUIREMENTS |
||
---|---|---|
Abrasion resistance |
Minimum 2000 cycles (Level 3) |
Complies |
Cut resistance |
Minimum 2.5 (Level 2) |
Complies |
Tear resistance |
Minimum 50 N (Level 3) |
Complies |
Puncture resistance |
Minimum 100 N (Level 3) |
Complies |
Flame resistance |
t Post-combustion ≤ 2s t Post-glow ≤ 5s (Level 4) The material does not leak The seams do not open |
Complies |
Convective heat resistance |
HTI24 ≥ 13 s (Level 3) |
Complies |
Radiant heat resistance |
Heat irradiation time > 22 s |
Complies |
Contact heat resistance |
At 250º C ≥ 10 s
|
Complies |
Lining material heat resistance |
At minimum 180ºC: Does not melt - Does not drip or burn |
Complies |
Shrinkage due to heat |
At 180ºC < 5% |
Complies |
Dexterity |
Minimum Level 1 (11 mm rod) |
Complies |
Resistance to breakage of seams |
>- 350 N |
Complies |
Glove removal time |
< 3 s |
Complies |
Water penetration resistance (optional) |
Levels 1 to 4 depending on the time it takes for the water to pass through the glove |
Complies |
Chemical penetration resistance |
Does not penetrate |
Complies |
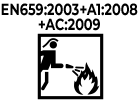
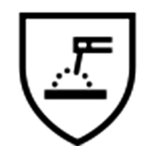
Requirements and test methods for welder's gloves. It classifies them into two types:
-
Type A general welder gloves.
-
Type B tact welder gloves. High desterity TIG welding case.
Warnings
At the moment there is no test method to determine the penetration of UV radiation through the materials from which the glove is made.
When gloves are intended for arc welding: These gloves do not provide protection against electric shock caused by faulty equipment or live work, and electrical resistance is reduced if the gloves are damp, dirty, or sweat-wet, which could increase the risk.
PROPERTY |
MINIMUM REQUIREMENTS |
||
---|---|---|---|
STANDARD NUMBER EN |
TYPE A |
TYPE B |
|
Abrasion resistance |
EN 388 |
2 (500 cycles) |
1 (100 cycles) |
Blade cut resistance |
EN 388 |
1 (index 1,2) |
1 (index 1,2) |
Tear resistance |
EN 388 |
2 (25 N) |
1 (10 N) |
Puncture resistance |
EN 388 |
2 (60 N) |
1 (20 N) |
Fire behavior |
EN 407 |
3 |
2 |
Contact heat resistance |
EN 407 |
1 (contact temperature 100ºC) |
1 (contact temperature 100ºC) |
Convective heat resistance |
EN 407 |
2 (HTI ≥ 7) |
- |
Resistance to small molten metal splashes |
EN 407 |
3 (25 drops) |
2 (15 drops) |
Desterity |
prEN420:1998 |
1 (diameter less than 11 mm) |
4 (diameter less than 6,5 mm) |
MINIMUM GLOVE LENGTH |
|||||||
---|---|---|---|---|---|---|---|
SIZE |
6 |
7 |
8 |
9 |
10 |
11 |
|
LENGTH |
300mm |
310mm |
320mm |
330mm |
340mm |
350mm |
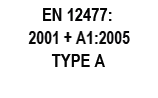
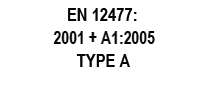
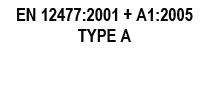
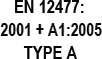
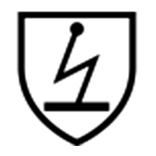
The sample must be conditioned at least 48 hours before the test and must be tested at an air temperature 23 +/- 1ºC and at a relative humidity of 25 +/- 5%.
For protective gloves with electrostatic dissipation, each individual measurement must meet the requirement: Vertical resistance, Rv < 1,0 x 108 Ω.
Warnings and additional information
-
Test results and test conditions in relation to the vertical resistance test.
-
The person wearing ESD protective gloves will be properly grounded, such as wearing appropriate footwear.
-
Protective gloves with electrostatic dissipation must not be removed from their packaging, opened, or put on or removed, when in a flammable or explosive atmosphere or when handling flammable or explosive substances.
-
The electrostatic properties of the protective gloves may be affected by aging, contamination or damage, and may not be sufficient for flammable oxygen-enriched atmospheres where additional evaluations are necessary.
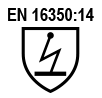
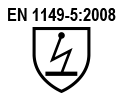

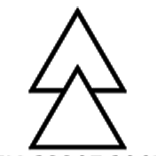
Insulating gloves from class 00 (500V) to class 4 (36000V).
Personal protective equipment EPI CAT III.
AZC category (resistant to Acids, ozone and very low temperatures).
RC category (resistant to Acids, oil, ozone and very low temperatures)..
MAXIMUM VOLTAGE (V) |
||||
---|---|---|---|---|
CLASS |
CATEGORY |
AC |
DC |
WEIGHT (gr) |
00 |
AZC |
500 |
750 |
90 |
0 |
RC |
1000 |
1500 |
200 |
1 |
RC |
7500 |
11250 |
270 |
2 |
RC |
17000 |
25500 |
450 |
3 |
RC |
26500 |
39750 |
560 |
4 |
RC |
36500 |
54000 |
800 |
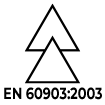
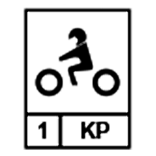
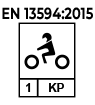
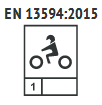
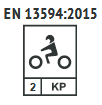
Application standard for motorcycle gloves in driving activities.
Nivel 1
For gloves designed to provide protection with few ergonomic restrictions associated with their use.
Nivel 2
For gloves providing greater protection than level 1. It may lead to greater weight restriction and difficulty in movement.
Requirements |
Level 1 |
Level2 |
---|---|---|
Minimum cuff length |
≥15mm |
≥50mm |
Fastening |
≥25N |
≥50N |
Tear resistance: palm and palm side of fingers |
≥25N |
≥35N |
Tear resistance: fist, back and back of fingers |
≥18N |
≥30N |
Tear resistance: forks |
≥18N |
≥25N |
Seam strength: main seams |
≥6N/mm |
≥10N/mm |
Seam strength: forks |
≥4N/mm |
≥7N/mm |
Minimum cut resistance index: palm side |
≥1,2 |
≥1,8 |
Minimum cut resistance index - back side |
No se requiere |
≥1,2 |
Minimum requirements for impact abrasion resistance: individual abrasion time |
≥3,0s |
≥6,0s |
Minimum requirements for impact abrasion resistance: average abrasion time |
≥4,0s |
≥8,0s |
Minimum requirements for impact attenuation: individual result |
opcional ≤ 9,0kN |
obligatorio ≤ 5,0kN |
Minimum requirements for impact attenuation: mean force transmitted |
opcional ≤ 7,0kN |
obligatorio ≤ 4,0kN |

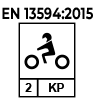
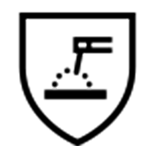
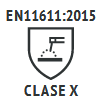
The user must adjust the garment through its closure systems, whether they are buttons, Velcro, slips or a mixture of them. You will never work with the garment unbuttoned.
Adapted additional PPEs must be worn to ensure maximum protection (face protection, helmet, gloves, footwear, ...). Please read the instructions for use and the safety information of the additional PPEs before use.
TYPE OF WELDER CLOTHING |
SELECCTION CRITERIA RELATED TO THE PROCESS: |
SELECCTION CRITERIA RELATED TO ENVIROMENTAL CONDITIONS: |
---|---|---|
Class 1 |
Manual welding techniques with slight spatter and droplet formation, for example: Oxygen gas welding / TIG welding / MIG welding / Micro plasma welding / Strong welding / Spot welding / MMA welding (with rutile coated electrode) |
Machine operation, for example of: Oxygen cutting machines / Plasma cutting machines / Resistance welding machines / Thermal spraying machine / Welding bench |
Class 2 |
Manual welding techniques with slight spatter and droplet formation, for example: Oxygen gas welding / TIG welding / MIG welding / Micro plasma welding / Strong welding / Spot welding / MMA welding (with rutile coated electrode) |
Machine operation, for example from: In confined spaces / Welding / Cutting under roof or in comparable forced positions |